Processes
- Polymer Processing
- Injection Molding Insert Molding Blow Molding Over Molding Metal Injection Molding Thermoforming
- Metal Casting
- Die Casting Castings & Forgings Wax Casting Lost Wax Casting Grey Iron Castings Centrifugal Casting Investment Casting Permanent Mold Sand Casting Shell Mold Casting Aluminum Investment Casting Brass Investment Casting Steel Investment Castings Titanium Investment Casting
- Machining
- Milling Turning EDM machining CNC Engraving Hole-making Tap Size Chart Drill Size Chart 5 axis machining Micro Machining CNC Cutting Metal Processes Ceramic Manufacturing Swiss Precision Machining
Materials
What is 5 Axis Machining – 5-axis CNC Machining Explain
5 Axis machining is a form of CNC manufacturing in which the part or tool is allowed to move along five different axes simultaneously, it is often used to make intricate parts or details. When it comes to the term “5-axis”, the coordinate system must be mentioned. The coordinate axis parallel to the spindle is defined as Z-axis, and the rotation coordinates around the X, Y and Z axes are A, B, and C respectively. The movement of each axis can be realized by the table or by the movement of the tool, but the direction is defined by the movement direction of the tool relative to the workpiece. Generally, five axis machining refers to the linear interpolation movement of any five coordinates in X, Y Z, A, B, and C. In other words, five axis refers to three linear axes X, Y Z axes plus any two rotating axes.
Compared with 3 axis machining, 5 axis machining centers can handle complex geometry and the tools can reach five different surfaces. In 5 axis CNC machining, the machine will avoid collision with the tool holder by tilting the cutting tool or table also allows better access to parts. Five axis machining is often used in the aerospace industry to process body parts, turbine parts and impellers.
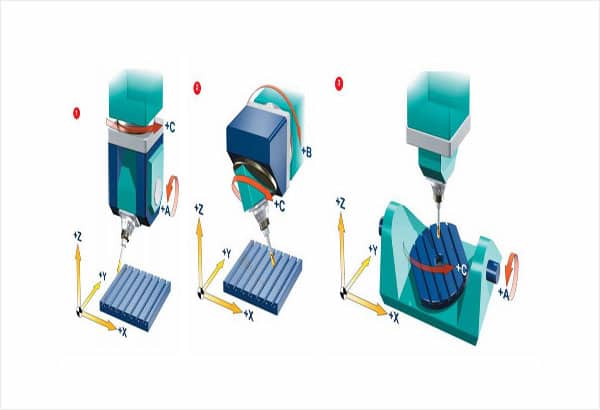
What is a 5 Axis Machine?
5 axis CNC machine is a machine tool controlled by a computer, which can move a tool or part on five different axes at the same time, usually adding two rotation axes to three linear axes (X, Y, Z). A, B and C rotation axes have different movement modes, which can meet the technical requirements of various CNC products. In the mechanical design of five-axis machining center, machine tool manufacturers have been committed to developing new motion mode to meet higher requirements.
Difference Between 3-Axis, 4-Axis and 5-Axis
4 Axis machining involves the same process as 3-axis machining, but it also includes rotation around the X-axis, which is called A-axis. 5 Axis machine involves all the axes of 4 axis machine, with the addition of another axis. 5 axis machines are able to hit five different sides of a part or more depending on the complexity at the same time which gets rid of unnecessary setups, so on a five axis machine, you still have a Z-axis moving up and down, X-axis is across, Y-axis is to the back of the machine, just like what acts on the three axis machine. But on a 5-axis machine, there is also a B-axis pivoting up the table rotates in a circle and an A-axis. The two additional rotary axes help the cutting tool approach the workpiece from all directions.
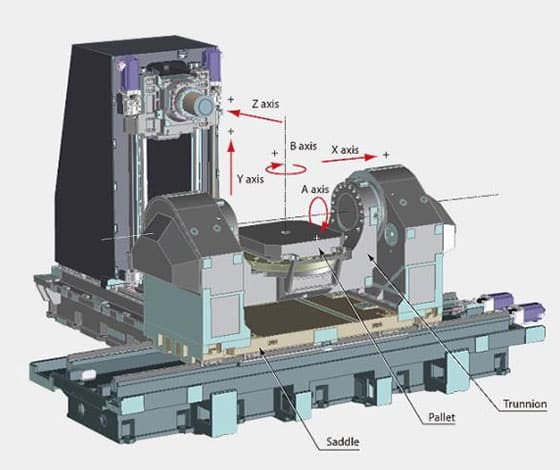
Why Use 5 Axis Machining?
What advantages or benefits make 5 axis machining services the preferred choice?
- Compared to the 3+2 axis machining or 5-sided machining, continuous 5-axis machining does not need stopping and starting between each reorientation of the tool and this brings its advantage in speed.
- Compared to 3D printing, 5 axis machining is still a competitive manufacturing method, as it can provide tight circularity tolerance and grow a feature to a near-net shape.
- The most notable advantage of 5 axis machining is it allows you to make your complex designs become true. With a 5 axis CNC machine, you can access the machining angles and arcs that can only be realized by a variety of settings and countless special fixtures before.
- 5 axis CNC machining only needs a single setup for the job, reducing the number of setups and eliminating the need to apply complex fixtures.
- The two rotational axes help you orient and make the part closer to the cutting tool, allowing you to use shorter cutting tools, which are not susceptible to vibration at very high cutting speed, and help you get the better surface finish.
- 5 axis machining reduces the assembly of parts, the workpiece can keep the precise alignment in one machining process, which improves the accuracy required to the product.
