Processes
- Polymer Processing
- Injection Molding Insert Molding Blow Molding Over Molding Metal Injection Molding Thermoforming
- Metal Casting
- Die Casting Castings & Forgings Wax Casting Lost Wax Casting Grey Iron Castings Centrifugal Casting Investment Casting Permanent Mold Sand Casting Shell Mold Casting Aluminum Investment Casting Brass Investment Casting Steel Investment Castings Titanium Investment Casting
- Machining
- Milling Turning EDM machining CNC Engraving Hole-making Tap Size Chart Drill Size Chart 5 axis machining Micro Machining CNC Cutting Metal Processes Ceramic Manufacturing Swiss Precision Machining
Materials
What Is Insert Molding
Insert molding is a kind of molding process in which the pre prepared inserts of different materials are put into the mold, then the resin is injected, and the molten materials are bonded with the inserts to form an integrated product.
In general, insert molding or overmolding requires that parts made of metal or other suitable materials (called inserts) be accurately placed in the mold, the mold is closed, and then plastic is injected into or around the insert. A typical application is an electrical connector that combines a machined metal pin or socket into a molded plastic housing. Most insert molded parts utilize metal parts, including handles, threaded inserts, or electrical contacts.
Some of the key benefits of using inserts on molded parts include:
- Improved strength
- A strong and reliable attachment point for assemblies (Inserts)
- More cost effective when compared to other inserting processes
- No significant mold changes required
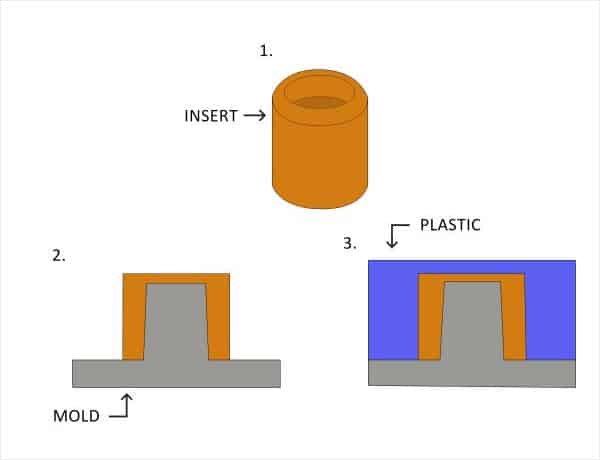
Insert Molding Process – How Does It Work
Injection molding is a process that is similar to injection molding in that it involves injecting molten raw material into a plastic mold – which is then solidified by cooling systems – and then opening the press and ejecting the molded parts. The only difference is that before the mold is closed, we must insert metals into the mold and begin all of the injection molding process as in injection molding.
Unlike injection molding, insert molding makes use of the same raw materials as injection molding, with the exception of metal that is introduced to the mold before it is closed. The same thermoplastics are employed for the intense version. The same mold steel, the same mold structure, and the same injection molding machine are used, with the exception of the occasional necessity to utilize a vertical injection molding machine for a unique instance. However, all of the injection molding machines are thermoplastic injection molding machines.
Some injection molding firms employ vertical/vertical injection molding presses, which use gravity to assist in the insert molding process by keeping the insert in place during mold closing, to produce their products. Insert into position during the sealing of the mold.
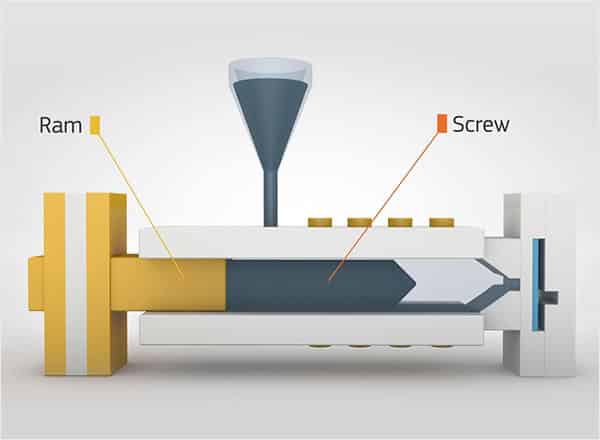
Why Choose Insert Molding
The main use of plastic insert molding is to create a strong and reliable molded part with a very low investment of money and time. This process helps to reduce assembly and labor costs. Also, it allows manufacturers to benefit from increased design flexibility without having to compromise on the structural integrity of the part. The reduced labor cost and the excellent quality control makes the insert molding process one of the best and least expensive methods to manufacture lightweight and compact parts that are reliable, durable, and fully functional.
Characteristics Of Insert Molding
- The combination of the formability and bending of resin and the rigidity, strength and heat resistance of metal can make a complex and exquisite metal plastic integrated product.
- In particular, the combination of the insulation of resin and the conductivity of metal is used, and the formed products can meet the basic functions of electrical products.
- The pre forming combination of multiple insert molded parts makes the post engineering of product unit combination more reasonable.
- Insert molding products are not limited to metal, but also cloth, paper, wire, plastic, glass, wood, wire ring, electrical parts, etc.
- For the rigid molding products and the bending elastic molding products on the rubber sealing pad, after the integrated products are made by injection molding on the substrate, the complex operation of arranging the sealing rings can be omitted, which makes the automatic combination of the later processes easier.
- Because it is the joint of molten material and metal insert, the gap of metal insert can be designed narrower and the reliability of composite product molding is higher than that of press in molding..
- Select appropriate resin and molding conditions, that is, for easily damaged products (such as glass, coils, electrical parts, etc.), the resin can also be used for sealing and fixation.
- The insert can also be completely sealed in the resin by selecting the appropriate mold structure.
- After inset molding, it can also be made into products with hollow grooves after core hole processing.
- With the combination of vertical injection molding machine, manipulator and insert assembly, most of the insert molding engineering can realize automatic production.
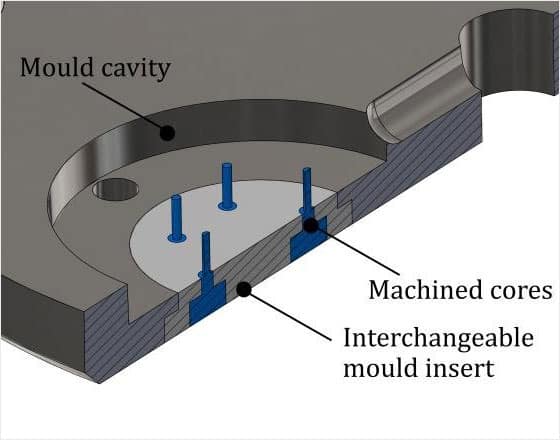
Benefits Of Insert Molding
- Using insert injection molding often results in a much stronger part and joint.
- It can provide some cost savings and work more efficiently.
- Insert injection molding improves manufacturability.
- Insert molding increases reliability and design flexibility.
- Insert molding reduces molding parts size, assembly, and labor costs.
- Improve part strength and structure
Insert Molding Applications
Insert molding applications are wide ranging with few limitations on material combinations, including:
- Knobs for appliances, controls and assemblies
- Encapsulated electronic devices and electrical components
- Military equipment
- Threaded fasteners
- Encapsulated bushings, tubes, studs, and posted
- Medical devices and instruments, such as needle hubs and tube valves
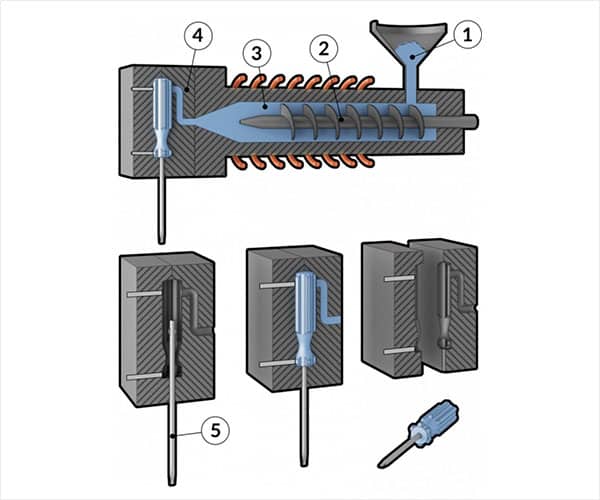
Insert Molding Vs Overmolding – What’s The Difference Between Insert Molding & Overmolding
Insert molding is just one of the processes used to mold plastic around a non-plastic item. Perhaps you are wondering how insert molding differs from overmolding. In simple terms, the key difference is that the number of steps required to achieve the end result, and the resulting item itself. Overmolding can be utilized as a double injection molding technique, although insert molding is more usually employed as a single injection molding method. Products created through overmolding (the twofold injection molding technique) have a relatively extended life span and frequently retain their original safety characteristics.