Processes
- Polymer Processing
- Injection Molding Insert Molding Blow Molding Over Molding Metal Injection Molding Thermoforming
- Metal Casting
- Die Casting Castings & Forgings Wax Casting Lost Wax Casting Grey Iron Castings Centrifugal Casting Investment Casting Permanent Mold Sand Casting Shell Mold Casting Aluminum Investment Casting Brass Investment Casting Steel Investment Castings Titanium Investment Casting
- Machining
- Milling Turning EDM machining CNC Engraving Hole-making Tap Size Chart Drill Size Chart 5 axis machining Micro Machining CNC Cutting Metal Processes Ceramic Manufacturing Swiss Precision Machining
Materials
What is Metal Processing? – Metal Processes
Metal processing, also referred to as metalworking, involves a wide variety of fabrication techniques for processing metal materials into goods, parts and components, from large parts of bridges, ships to tiny components of engines, jewelry and watches. Metal processing is the base of metal production, each metal manufacturing method includes some form of metal processing operations, which usually reshapes a metal blank or material into a part with specific geometry or dimensions.
Common Metal Processing Techniques & Methods
1. Casting
Metal casting is a process that pouring molten metal into a mold cavity, and the metal takes on the shape of the cavity when it cools and solidifies. Based on the drawings of products, a pattern that conforms to the external shape of the finished casting part is constructed. The process of metal casting involves making a pattern of the desired part, making the mold & cores, melting and refining the metal, pouring metal into the mold cavity, cooling the metal casting, removing the casting and extra metal materials. Most casting processes are adopted to produce initial metal ingot or near-finished shape metals preparing for the following fabrication. Metal casting can be divided into several different types.
- Sand casting: the most widely used metal casting process, which is characterized by using sand as the mold material.
- Permanent mold casting: the mould made of iron or steel can be used repeatedly.
- Die casting: the molten metal is forced into a metal mold under pressure, aluminum is the most common metal in die casting. Other materials including zinc, copper, etc.
- Investment casting: a wax pattern is made of each casting to be fabricated and covered with refractory which will form the mold into which the metal is poured.
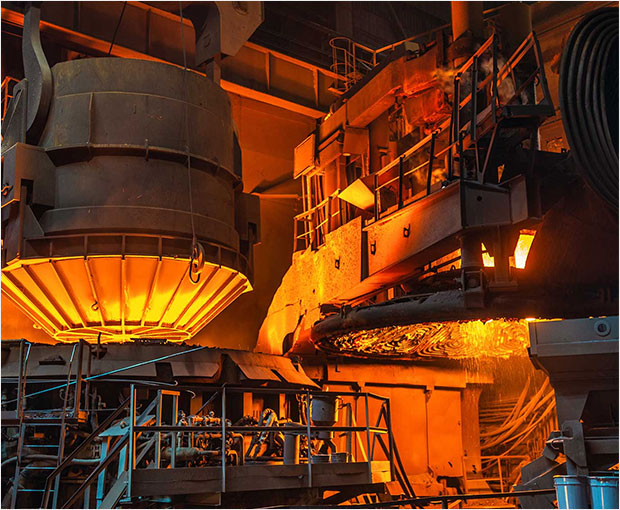
2. Deformation
Deformation process including metal forming and sheet metalworking. Large deformations and shape changes are defined as the bulk deformation processes. Sheet metalworking usually works with metals in the forms of sheets, strips, and coils, and these operations are performed using a punch and a die to form the object.
- Forging: using compressive forces to pre-formed blocks of metals at high temperatures, in one or more discrete pressing steps. The shape of the final product is determined by the geometry of the die cavities. Forging operations may pose a high risk of tearing when workers handle forged parts or trim flash or unwanted edges on parts.
- Rolling: a cost-efficient metal processing method to reduce the cross-sectional area of a metal section, generally used for producing flat products.
- Extrusion: a metal forming process in which pushing the material through or around a die using a mechanical or hydraulic press, suitable for the formation of complex cross-sections in one piece of metal.
- Bending: a metal manufacturing process that deforms the metal to make the workpiece bed at an angle and form different shapes along a straight axis in ductile materials when applying force to the object, ideal for bending sheet metals to a v-shape, u-shape, channel shape, and more.
- Drawing: a metalworking process that applying tensile forces to stretch the materials and achieve the desired shape and thickness. Drawing can extend the length of metal and reduce the thickness.
- Shearing: also known as die cutting, a metal fabrication process that straight lines are cut into sheet metal with cutting blades, without the formation of chips or the use of burning or melting. Blanking, piercing, and trimming are all shearing-type operations.
3. Material removal
Material removal processes refer to the techniques that removing extra material from the raw block to get the desired shape and dimensions.
- Turning: a form of the machining process. It fixes the cylindrical workpiece in the chuck and rotates. At the same time, the tool is fed into the workpiece and the material is removed to obtain the required turned parts. Turning can be carried out outside or inside the workpiece to produce tubular parts of various geometries.
- Drilling: a metal cutting process that uses a drill bit to cut a hole with a circular cross-section in solid materials, various drill bits are used, depending on the material to be cut and the requirement of the hole.
- Milling: one of the most common manufacturing processes, a machining process using rotary cutting tools to remove materials from a workpiece by feeding the cutter into the part. Milling operations need to be carried out on a milling machine or machining centers.
- Grinding: an abrasive machining process that using a grinding wheel or grinder to remove material from a workpiece. When the grinding wheel turns, it cuts material off the part while creating a smooth surface.
- EDM: electrical discharge machining, also known as spark machining, is a metal fabrication method for precisely removing materials from conductive materials using an electrode.
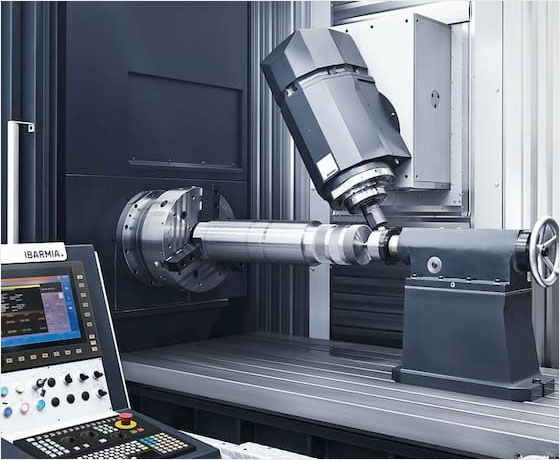
4.Other metal processes
- Heat treatment: heating and cooling metal that remains solid is usually an integral part of metal product processing. It almost always involves changes in the crystal structure of metals, thereby changing their properties.
- Hardening: a metallurgical metalworking process used to improve the hardness of metals, including heating the component above the critical temperature, maintaining it for one hour per inch of thickness at this temperature, cooling at a rate fast enough to transform the material into a harder and stronger structure, and then tempering.
- Welding: a process by which two pieces of metal can be joined together. There are lots of different welding methods, such as Shielded Metal Arc Welding, Submerged Arc Welding, Flux-Cored Arc Welding, Gas Metal Arc Welding, and Gas Tungsten Arc Welding.