Processes
- Polymer Processing
- Injection Molding Insert Molding Blow Molding Over Molding Metal Injection Molding Thermoforming
- Metal Casting
- Die Casting Castings & Forgings Wax Casting Lost Wax Casting Grey Iron Castings Centrifugal Casting Investment Casting Permanent Mold Sand Casting Shell Mold Casting Aluminum Investment Casting Brass Investment Casting Steel Investment Castings Titanium Investment Casting
- Machining
- Milling Turning EDM machining CNC Engraving Hole-making Tap Size Chart Drill Size Chart 5 axis machining Micro Machining CNC Cutting Metal Processes Ceramic Manufacturing Swiss Precision Machining
Materials
Castings and Forgings
Forging is used to train metal, and casting is used to melt and mold metal. Both processes are process of molding the shape of metal, both of which are very similar in that they use molds, but the advantages and disadvantages of each method and the characteristics of the products made are completely different.
This time, we will explain the difference between forging and casting, from the characteristics of each method to the difference between products made of both forging and casting such as car wheels, golf clubs, and engagement rings.
Difference between Forging and Casting
Let’s check the difference from the rough process and features of each forging and casting process.
In order to compare this time as easy to understand as possible, forging is based on “mold forging” using molds, and casting is based on the characteristics of “sand mold casting” using molds made of sand, and forging and casting are compared.
The forging and casting processes are as follows:
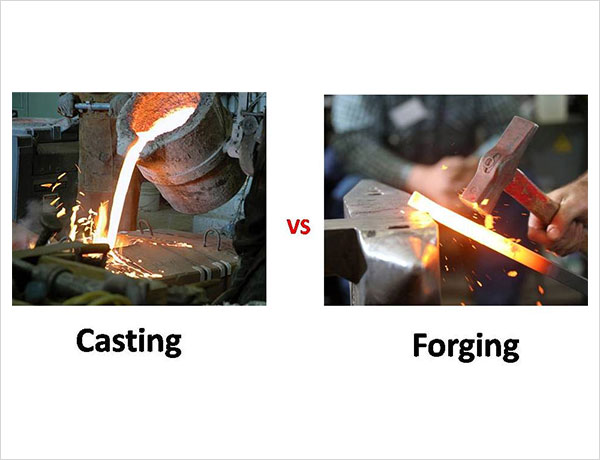
What is Casting?
Casting is a processing method in which a material (mainly metals such as iron, aluminum alloy, copper, brass, etc.) is heated at a temperature higher than the melting point to make a liquid, then poured into a mold, cooled, and hardened into the intended shape. The characteristic of casting is the high degree of freedom in shape and size. You can also make many products with one casting.
Depending on the type of mold, there are sand molds made by hardening sand, molds made by scraping metal, resin molds and plaster molds. Molds are called molds, and castings are casts. Casting can produce large quantities of parts with complex shapes at low cost, and there are advantages such as being able to make hollow parts and there is no limit on size, and various things such as applications and sizes can be made by materials and manufacturing methods.
Casting features and benefits
Advantages of Casting
As a feature of the die casting method, it is possible to make thin or complicated shapes due to its high dimensional accuracy. In addition, since it can be mass-produced, significant cost reduction can be expected.
- Mass production is possible
- High strength of casting
- Easy to utilize the characteristics of metal
- It is also possible to manufacture thin products and highly designed products.
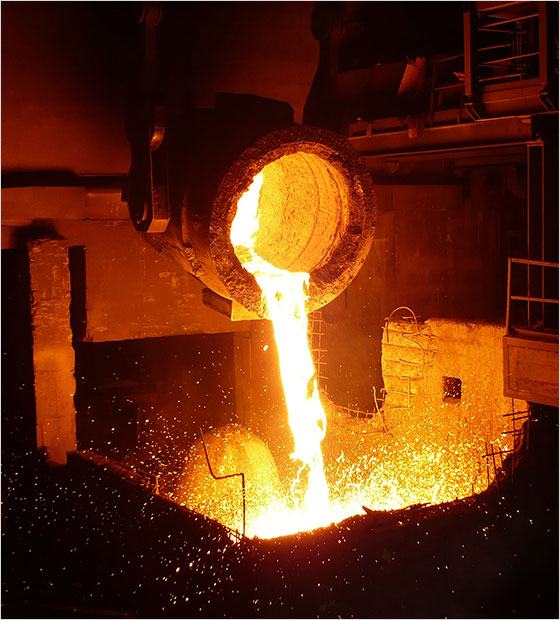
Casting Process
1.Melt the material
The material is melted at a high temperature such as in an electric furnace to make it a liquid.
2.Pour the melted material into the mold
The work of taking out the liquefied material is called hot water, and the work of pouring it into a mold is called hot water pouring.
3.Cool and harden the poured material
Casting does not apply force to the object, which can leave stress inside the object as it cools, which can reduce its strength.
4.Take it out of the mold and complete the molding
The mold used for casting is called a mold, and it is handled slightly differently from the mold used in other processing methods. First, for the mold, create the original mold called a wooden mold or foam mold, and then create a mold for manufacturing called a sand mold based on it. Since sand molds that have been used once are basically disassembled, it is possible to manufacture complex shapes that are difficult to remove by casting.

Materials and Applications for Castings
Materials used in castings include cast iron, steel, aluminum alloys, copper alloys, magnesium alloys, zinc alloys, nickel alloys and titanium alloys. Table 2 shows the materials used for casting and examples of their uses.
Casting Material | Application |
---|---|
Min Feature Size | Cylinder block, diesel cylinder head, camshaft, oil pump housing, brake rotor, differential case, axle housing, seat spring, bulldozer case, forklift mission cases, torque converter cases, etc. |
Steel Casting | Rollers, roll housings, caterpillars, gears, crushers, hammers for crushers, crankshafts, crank throws, stun frames, rudder horns for ships, couplers for railways, brake shoes, etc. |
Copper Alloy | Faucet valves / fittings, drain fittings, hydraulic / pneumatic valves, pump fuselage, seawater pumps, bells, Buddha statues, bells (Buddha tools), book ends, trays, bronze statues, bronze engravings, etc. |
Aluminum Alloy | Cylinder block, transmission case, cylinder head, engine mount bracket, converter housing, exterior, garden chair / bench, gate, fence, etc. |
Magnesium Alloy | Laptop housing, mobile phone housing, single-lens reflex camera housing, video camera housing, lens frame for projectors, etc. |
Zinc Alloy | Switchboard handle, flange shaft for copier, refrigerator handle for business use, lock operation lever for vending machine, finder parts for camera, connector parts, etc. |
Nickel Alloy | Turbine blades, valve bodies, Pelton runners, etc. |
Titanium Alloy | Turbine blades for power generation, pacemakers, artificial joints, golf club heads, etc. |
What is Forging?
Forging is a technique that increases strength by hitting metal and applying pressure, and molds it into the shape of the object. Since this tapping work is “trained”, this manufacturing method is called “forging” because it is “trained and made”.
Forging is characterized by crushing internal voids by hitting metal with a hammer or press, miniaturizing crystals, and increasing strength by adjusting the direction of crystals. It has been known since ancient times that iron removes the intervention by beating it and strengthens it. Due to its properties, it is often used in products that require strength, and it is also used for kitchen knives and pliers that are familiar to daily life from parts such as automobiles and aircraft.
Advantages of forging
Since the material is prepared according to the forging mold and molded by tapping, there is less material than the method such as metal shaving. For this reason, it is also suitable for mass production, and has been used in many automotive parts.
- Save materials
- Dense material structure and no internal defects
- Since it is close to the final shape, the cutting process of the later process can be omitted.
- Improves mechanical properties (tension strength and hardness)
- A train line (metal flow) that matchs the product shape can be obtained.
- Things of the same shape can be mass produced
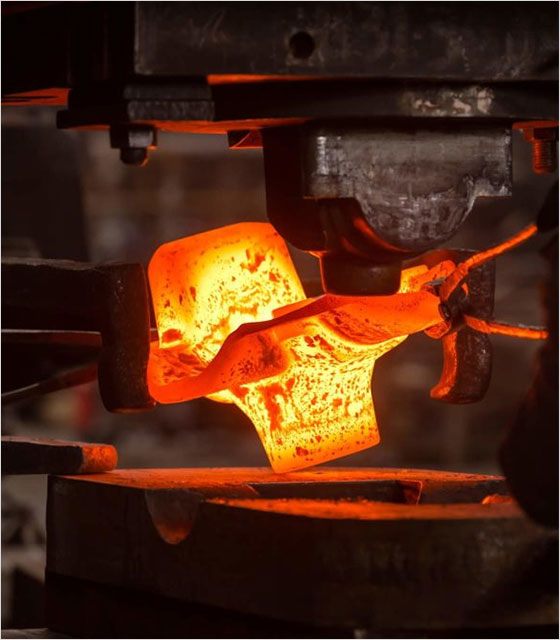
Forging Process
1.Cutting and installation of material
Place the material you want to mold in the position to be pressed with the mold. At this time, if the material is too large for the mold, it should be cut in advance to make it easier to process.
2.Apply force by compression / impact
When applying force by compression / impact, the type is divided into “cold / warm / hot” depending on the temperature at which the material is processed. The stronger it is processed at a temperature closer to room temperature, but the more difficult it is for the material to deform, which tends to make complicated processing difficult.
3.Apply more force
The compressed / impacted metal has high strength because air bubbles inside the metal are crimped to eliminate defects, and the crystals become finer and the crystal directions are aligned. The line formed by the crystal structure with the same direction at this time is called the forging line (metal flow line / fiber flow line). Since forging is performed while maintaining the strength of the material, the process of applying force is important, but it is said that forging costs more to manufacture than other processing methods because of this process.
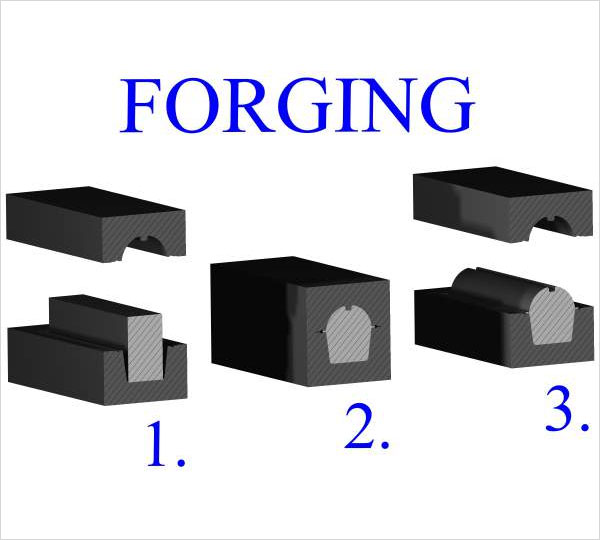
4.Take out from the mold and complete molding
Products taken out of the die are usually finished by further cutting, but if high-precision forging such as net shape or near net shape is used, post-processing may not be necessary.
Materials and Applications for Forgings
Casting Material | Application |
---|---|
Brass | Various valves, Mechanical parts, Gas equipment, Solenoid valves, High-pressure pumps / cylinders, Faucet fittings, Air conditioners, Outdoor units, Marine parts, Electrical equipment, Steam traps, Lasers, robot equipment, etc … |
Copper | Electrical equipment such as transformer equipment, Electrical equipment such as crimp terminals, Electrical equipment such as connection terminals, Heat radiator, cryopump parts Lightning rod parts, Chemical industry parts, Battery terminals, Electric heating equipment, etc … |
Steel Alloy | Hydraulic cylinders, Various industrial machine parts, Pumps, Compressors, Shafts, Hydraulic jacks, Crankshafts, Bolted joints etc. |
Aluminum Alloy | Structural materials for buildings, etc. Parts for automobiles, railroad vehicles, etc. Aircraft parts, air conditioner parts, electronic equipment parts, office equipment, laser equipment, robot equipment, etc … |
Various special materials | Suspension 630: Bolt / Shaft / Turbine etc Inconel 625: Marine equipment parts, high temperature heating pipes and exhaust system parts etc Inconel 718: Turbine / diesel engine parts for aerospace parts and submarines, etc Monel 400: Marine equipment parts, industrial heat exchangers, X-ray equipment, etc Magnesium: Automotive parts / Electronic devices such as PCs / Welfare equipment etc 64 Titanium: Aerospace parts / Medical equipment / Bicycle parts etc Pure iron: Motor parts / magnetic blocking material / electromagnet iron core etc |
Difference Between Forging and Casting
Forging is a processing method in which metal is struck and molded, and casting is a processing method in which metal is melted into a liquid and poured into a mold. Both can make parts of the same shape, but even if they look the same, there is a big difference between the two.
Forging | Casting | |
---|---|---|
Processing method | Molding by compressing with a mold | Pour metal melted in muddy into a mold and mold |
Advantages | When compressed, the crystals inside the metal are aligned, resulting in increased strength. | Even complicated shapes can be processed relatively easily |
Disadvantages | Need a gradient to remove from the mold. Useless fleshing may be required depending on the shape | Due to the problem of strength, it is necessary to secure a certain wall thickness, which makes the weight heavier than forging. |
Cost | High cost (depending on the shape, dimensions and specifications of the part) | The cost is low (depending on the shape, dimensions, and specifications of the parts) |
Presence or absence of stress | No stress remains | Internal stress may remain |