Processes
- Polymer Processing
- Injection Molding Insert Molding Blow Molding Over Molding Metal Injection Molding Thermoforming
- Metal Casting
- Die Casting Castings & Forgings Wax Casting Lost Wax Casting Grey Iron Castings Centrifugal Casting Investment Casting Permanent Mold Sand Casting Shell Mold Casting Aluminum Investment Casting Brass Investment Casting Steel Investment Castings Titanium Investment Casting
- Machining
- Milling Turning EDM machining CNC Engraving Hole-making Tap Size Chart Drill Size Chart 5 axis machining Micro Machining CNC Cutting Metal Processes Ceramic Manufacturing Swiss Precision Machining
Materials
Investment Casting (Lost Wax Casting) – What Is Investment Casting?
Investment casting is often referred to as precision casting or lost wax casting. This technique is approximately 5000 years old and has been utilized throughout the ages to make art and jewelry. Investment casting uses a shell created by a wax pattern, consisting of ceramic, plaster, or plastic. The wax design will be melted and removed in an oven, and metal will be poured into the casting shell. Casting for investment provides accurate components while reducing waste materials, energy, and subsequent machining. The manufacturing of complicated components may also be assured. For design engineers, this makes the investment casting process very helpful. Determine which casting processes are best appropriate for producing a product, such as design criteria, costs, and feasible manufacturing.
The Investment Casting Process – How Does Investment Casting Work?
- Developing The Pattern – It employs a pattern with the same features as the final component, except a thermal contraction tolerance. Wax patterns are usually created using a metal injection die.
- Making The Tree And Mounting The Wax Patterns – After creating a wax design, it is joined with other wax components to create the gate and runner metal delivery system. Multiple wax patterns may be processed using a single tree, depending on the size and configuration of the required finish component.
- The Making of the Mold Shell – The whole wax pattern assembly is immersed in a ceramic slurry, coated with sand stucco, and dried. Wet dipping and stuccoing cycles are continued until a shell of the appropriate thickness is achieved. The thickness is determined in part by the size and design of the product. When the ceramic shell dries, it becomes strong enough to hold the molten metal during casting.
- Removal of Wax – To remove the majority of the wax, the whole assembly is put in a steam autoclave. In a furnace, any residual wax absorbed into the ceramic shell is burnt away. The remaining wax pattern and gating material have been entirely removed at this stage, leaving the ceramic mold with a hollow in the form of the required cast component. This high-temperature process also improves the ceramic material’s strength and stability. Furthermore, it aids in reducing the reactivity of the shell and metal during pouring.
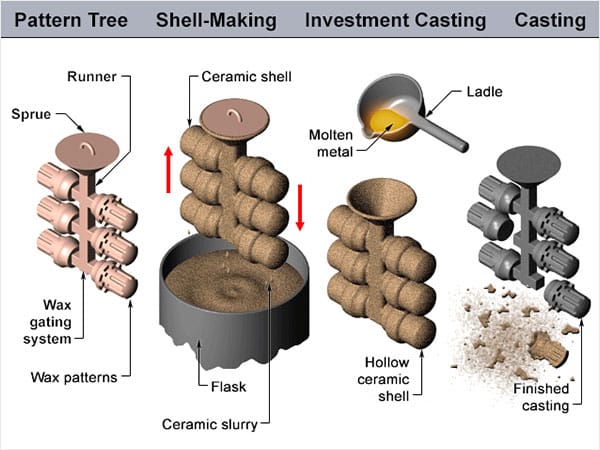
- Casting and Melting – Metal casting is created by heating the mold to a particular temperature and filling it with molten metal. Almost any alloy may be created using this method. Depending on the alloy chemistry, either air melting or vacuum melting may be used. When reactive components are included in the alloy, vacuum melting is used.
- Operations at the End – When the casting has sufficiently cooled, the mold shell is knocked away from the casting in a knockout operation. The gates and runners are cut from the casting, and final post-processing sandblasting, grinding, and machining is done if required to complete the casting dimensionally. Non-destructive testing may consist of fluorescence penetrant, magnetic particle, radiographic, or other examinations. Before shipping, final dimensional inspections, alloy test results, and NDT are confirmed.
Applications Of Investment Casting Process
Investment castings have a plethora of uses. However, these metal components are most often used in the aerospace, power generation, firearm, automobile, military, commercial, food service, gas and oil, and energy sectors. Cast components, for example, are used in the guns industry for rifle receivers, triggers, hammers, and other precision parts. Investment castings are also utilized by makers of beverage industry equipment and worldwide pressure relief valve manufacturers in the oil and gas sector. As a consequence, regardless of your sector, if your company can profit from the benefits of investment cast parts and components, they may be the ideal metal choice for any of your projects.
The Different Types of Investment Casting Materials
Investment casting may be used to create a broad range of goods and prototypes, but it is critical to choose the right investment casting material for your purpose. The appropriate material allows you to achieve the required functionality while saving money on resources, eliminating undesired casting flaws and limiting the need for additional operations once the casting is finished. During the material selection process for investment casing, there is a wide variety of alloys to choose from. These include:
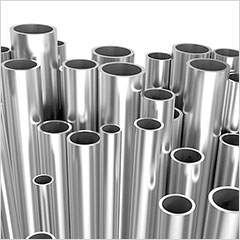
Stainless Steel
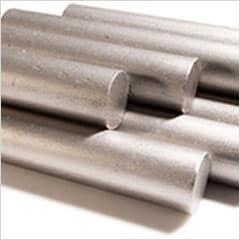
Low Alloy Steel
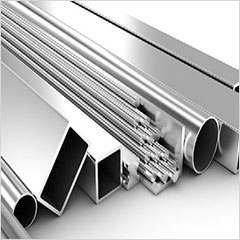
Aluminum Alloy
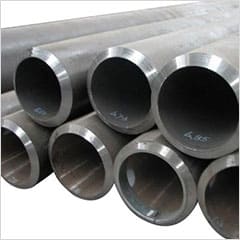
Carbon Steel
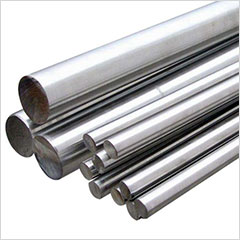
Super Alloy
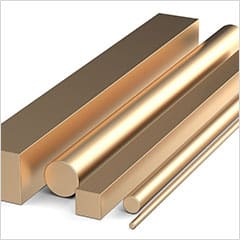
Copper Alloy
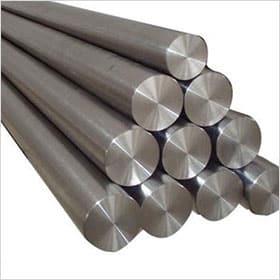
Cast Iron
Investment casting materials have varying characteristics and applications, which is why it is critical to choose the appropriate casting material for your application. Proper material selection will eventually assist you in achieving the intended functionality of your design while reducing expense and waste.
Final components may have smooth surfaces and dimensional accuracy while being lighter, thinner, or have other advantageous characteristics. Material selection has a significant impact on which characteristics may be effectively integrated into your component.
Advantages Of Investment Casting Process
- Investment casting comes in a broad variety of sizes. Even though the majority of investment castings are tiny, the investment casting technique may create castings weighing more than 1,000 pounds. This capacity is restricted to a small number of investment casters and requires specialized handling. Most cast components weigh between ounces and 20 pounds.
- Investment casting allows for reliable and repeatable tight tolerances, as well as complex passageways and curves. Many of these combinations are impractical to manufacture. For example, where machine tools are unable to reach. Obtaining net-shape or nearly-net-shape cast components may significantly decrease post-cast processing expenses.
- Investment casting is an excellent alternative to welding or fabrication. A single casting may include several components. The greater the number of components integrated, the greater the production efficiency. Converting multi-piece components to a single investment casting usually results in higher dimensional accuracy and lower part complexity.
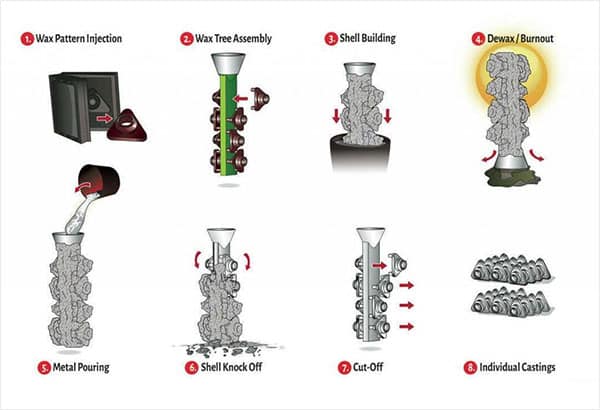
Disadvantages Of Investment Casting
The major drawback is the total expense, which is particularly significant for short-run manufacturing. A few of the explanations for the increased cost include specialized equipment, expensive refractories and binders, numerous procedures to create a mold, a lot of work, and the occurrence of minor errors. However, the cost is still cheaper than machining the identical component from bar stock; for example, gun production has shifted to investment casting to reduce the cost of making handguns.
- Casting objects that need cores may be challenging.
- This technique is costly, typically restricted to tiny castings, and may be problematic when cores are involved.
- Holes must be no smaller than 1/16 in. (1.6 mm) in diameter and no deeper than 1.5 times the diameter.
- Investment castings need longer production cycles than other casting techniques.
- Because many process variables influence the quality of the mold and casting, the quality management system is difficult to implement.
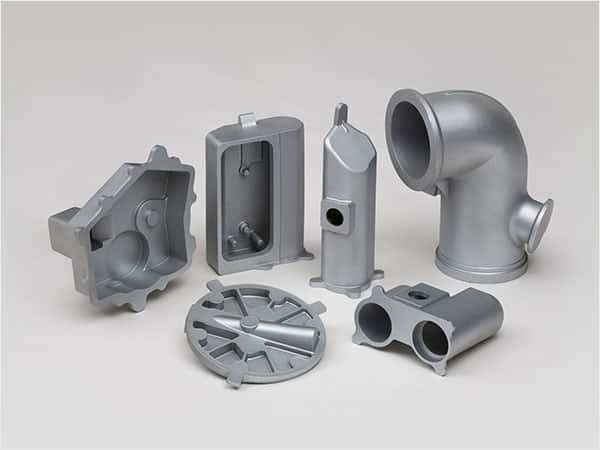