Processes
- Polymer Processing
- Injection Molding Insert Molding Blow Molding Over Molding Metal Injection Molding Thermoforming
- Metal Casting
- Die Casting Castings & Forgings Wax Casting Lost Wax Casting Grey Iron Castings Centrifugal Casting Investment Casting Permanent Mold Sand Casting Shell Mold Casting Aluminum Investment Casting Brass Investment Casting Steel Investment Castings Titanium Investment Casting
- Machining
- Milling Turning EDM machining CNC Engraving Hole-making Tap Size Chart Drill Size Chart 5 axis machining Micro Machining CNC Cutting Metal Processes Ceramic Manufacturing Swiss Precision Machining
Materials
What Is Sheet Metal Forming
Sheet metal forming is a process where pieces of sheet metal are modified to its geometry. The applied process provides a force that causes the material to deform as a result of the stress. This in turn allows for the sheet to be bent and stretched into a variety of complex shapes. The desired shape is achieved through plastic deformation, without undergoing any machining like milling. The sheet metal forming process can be used to produce a wide variety of different components. These components range in weight from several hundred grams up to several tons.
Common Sheet Metal Forming Process
Sheet metal forming processes are those in which force is applied to a piece of sheet metal to modify its geometry rather than remove any material. The applied force stresses the metal beyond its yield strength, causing the material to deform plastically but not to fail completely. By doing so, The sheet can be bent or stretched into a number of intricate shapes as a result of this process. Sheet metal forming processes include the following:
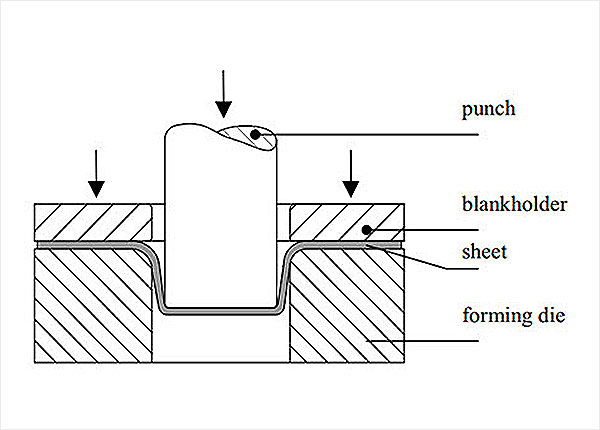
1.Crimping
Crimping is a sheet metal forming process. After the initial production of sheet metal, there are usually sharp edges with “burrs”. The purpose of crimping is to smooth the sharp and rough sheet metal edges to meet the use requirements of the project.
2.Bending
Bending is another common sheet metal forming process. Manufacturers usually use brake press or similar mechanical press for metal bending. The sheet metal is placed on the die, and the punch is pressed down on the sheet metal. The huge pressure makes the sheet metal bend. A bend can be characterized by several different parameters:
- Bend line. The straight line on the surface of the sheet, on either side of the bend, that defines the end of the level flange and the start of the bend.
- Outside mold line. The straight line where the outside surfaces of the two flanges would meet, were they to continue. This line defines the edge of a mold that would bound the bent sheet metal.
- Flange length. The length of either of the two flanges, extending from the edge of the sheet to the bend line.
- Mold line distance. The distance from either end of the sheet to the outside mold line.
- Setback. The distance from either bend line to the outside mold line. Also equal to the difference between the mold line distance and the flange length.
- Bend axis. The straight line that defines the center around which the sheet metal is bent.
- Bend length. The length of the bend, measured along the bend axis.
- Bend radius. The distance from the bend axis to the inside surface of the material, between the bend lines. Sometimes specified as the inside bend radius. The outside bend radius is equal to the inside bend radius plus the sheet thickness.
- Bend angle. The angle of the bend, measured between the bent flange and its original position, or as the included angle between perpendicular lines drawn from the bend lines.
- Bevel angle. The complimentary angle to the bend angle.
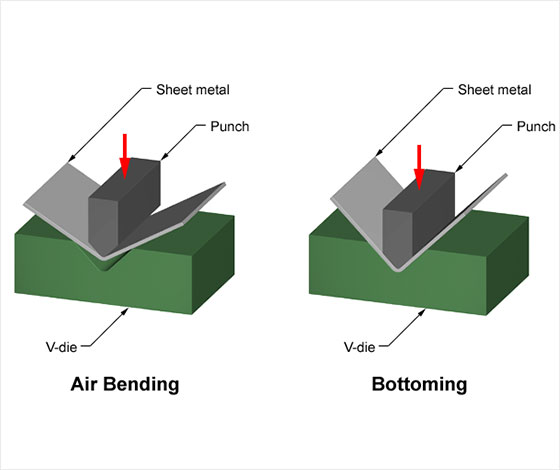
3.Ironing
Sheet metal can also be ironed to obtain uniform thickness. For example, many beverage cans are made of aluminum. The aluminum metal plate is too thick for the beverage can in the original state, so it needs to be ironed to make it thinner and more uniform.
4.Laser Cutting
Laser cutting has become a more and more common sheet metal forming process. When the sheet metal is exposed to high power and high density laser, the heat of the laser melts or vaporizes the sheet metal in contact with it, forming a cutting process. This is a faster and more accurate cutting method, which is automatically executed by computer numerical control (CNC) laser cutting machine.
5.Stamping
Stamping is a common sheet metal forming process, which uses stamping machine and die group to punch holes in sheet metal. During machining, the sheet metal is placed between the punch and the die, and then the punch is pressed down and passes through the sheet metal, thus completing the punching process.
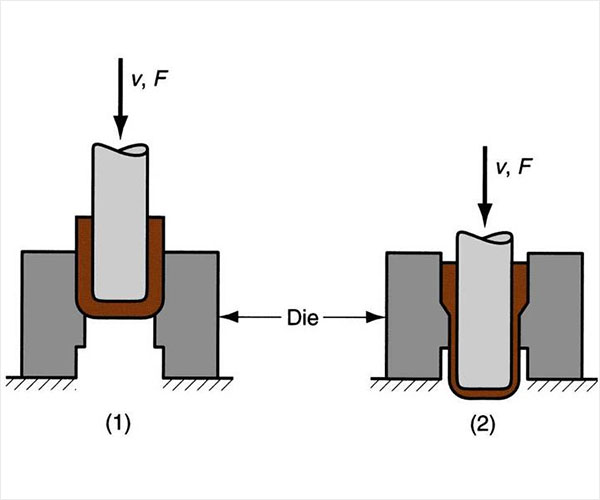
Applications Of Sheet Metal Forming
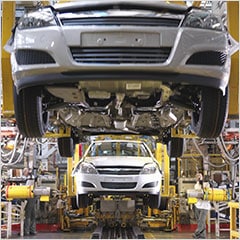
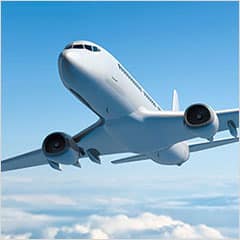
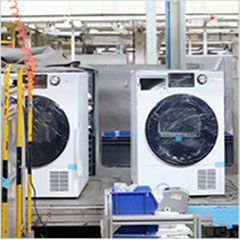
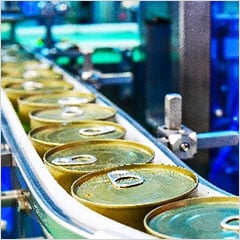
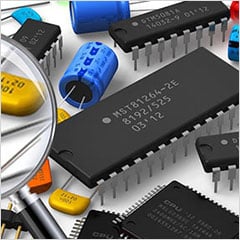
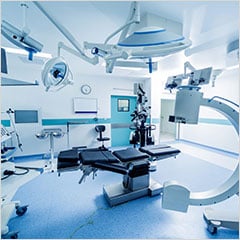