Processes
- Polymer Processing
- Injection Molding Insert Molding Blow Molding Over Molding Metal Injection Molding Thermoforming
- Metal Casting
- Die Casting Castings & Forgings Wax Casting Lost Wax Casting Grey Iron Castings Centrifugal Casting Investment Casting Permanent Mold Sand Casting Shell Mold Casting Aluminum Investment Casting Brass Investment Casting Steel Investment Castings Titanium Investment Casting
- Machining
- Milling Turning EDM machining CNC Engraving Hole-making Tap Size Chart Drill Size Chart 5 axis machining Micro Machining CNC Cutting Metal Processes Ceramic Manufacturing Swiss Precision Machining
Materials
What Is SLS (Selective Laser Sintering)?
Selective Laser Sintering (SLS) is one of the technologies used by today’s 3D printers. SLS it’s the process of turning digital designs into three-dimensional objects that produces accurate prototypes and functional production parts in as fast as 1 day.. SLS was developed at the University of Texas in Austin, by Carl Deckard and colleagues. The reason why Selective Laser Sintering was trusted by engineers and manufacturers across different industries for its ability to produce strong, functional parts. It mainly uses metal powder as material, and its principle is laser sintering powder material, so that the powder material can be combined to form.
How Does Selective Laser Sintering work?
The working process of SLS is similar to that of 3D Printing, uses the principle of stack forming, which is based on the powder bed. The difference is that 3D Printing uses the spray binder to bond the powder, while SLS uses the infrared laser to sinter the powder. First, lay a layer of powder material with powder roller, and heat it to a certain temperature just below the sintering point of the powder through the constant temperature facility in the printing equipment. Then, the laser beam irradiates the powder layer to make the temperature of the irradiated powder rise above the melting point for sintering and bonding with the formed part below. When a layer is sintered, the printing platform will drop to a height of layer thickness, and the powder laying system will lay new powder materials on the printing platform, and then control the laser beam to irradiate again for sintering, so as to cycle and stack layer by layer until the printing of the whole three-dimensional object is completed.

Why Use SLS?
SLS machine can print a variety of high-quality materials from flexible plastics to food grade ceramics, such as plastics, glass, ceramics and even metals, and SLS can also print customized products in 3D. Moreover, since objects printed with SLS do not rely on molds or require other tools, this manufacturing method is also useful for anyone who wants to print highly complex or particularly fine objects. SLS uses thermoplastic and elastomeric materials to build excellent mechanical components.
The Advantages Of SLS
Selective Laser Sintering molding method has the characteristics of simple manufacturing process, high flexibility, wide range of material selection, low material price, wide application, low cost, high material utilization rate and fast molding speed.
The Disadvantages Of SLS
It costs a lot to maintain SLS machine. And insufficient mechanical properties, especially low elongation, rarely can be directly applied to the manufacturing of metal functional parts. Also, complicated auxiliary process is needed.
The Application Of SLS
Recent advances in machinery, materials, and software have made SLS printing accessible to a wider range of businesses, enabling more and more companies to use these tools that were previously limited to a few high-tech industries. SLS 3D is mainly used in the foundry industry, rapid prototyping to small-batch, bridge, or custom manufacturing and can be used to directly make fast mold. Four cylinder engine generated by SLS technology.
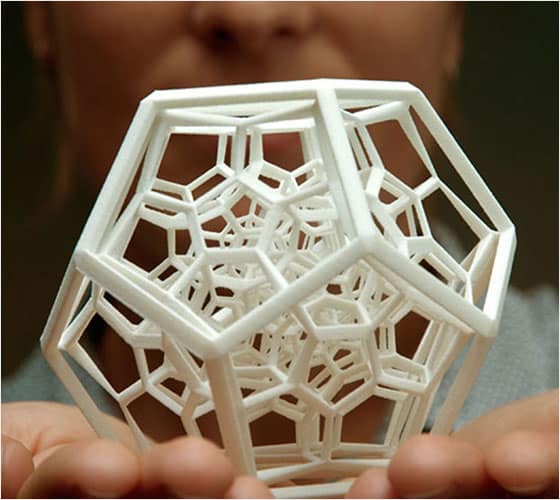
Material type: | Powder (Polymer) |
Materials: | Thermoplastics such as Nylon, Polyamide, and Polystyrene; Elastomers; Composites |
Max part size: | 22.00 x 22.00 x 30.00 in. |
Min feature size: | 0.005 in. |
Min layer thickness: | 0.0040 in. |
Tolerance: | 0.0100 in. |
Surface finish: | Average |
Build speed: | Fast |
The Most Reliable SLS 3D Printer Manufacturer
Protolabs is a leading 3D printing, CNC machining, sheet metal fabrication, and injection molding manufacturer and supplier in Minnesota. They offer the fastest and most comprehensive digital manufacturing service in the world. Their SLS equipment comprises sPro140 machines with the greatest build volumes of sintering in the world and completely digital high-speed scanning systems, unrivaled process consistency as well as closed powder mixing and delivery systems for assured parts quality.