Processes
- Polymer Processing
- Injection Molding Insert Molding Blow Molding Over Molding Metal Injection Molding Thermoforming
- Metal Casting
- Die Casting Castings & Forgings Wax Casting Lost Wax Casting Grey Iron Castings Centrifugal Casting Investment Casting Permanent Mold Sand Casting Shell Mold Casting Aluminum Investment Casting Brass Investment Casting Steel Investment Castings Titanium Investment Casting
- Machining
- Milling Turning EDM machining CNC Engraving Hole-making Tap Size Chart Drill Size Chart 5 axis machining Micro Machining CNC Cutting Metal Processes Ceramic Manufacturing Swiss Precision Machining
Materials
Jetted photopolymer is an additive method that combines Inkjet Printing and Stereolithography technologies. The process of developing each layer is similar to that of inkjet printing, it employs an array of inkjet print heads to deposit small droplets of build material and support material to build each layer of a component. The build material, like in Stereolithography, is a liquid acrylate-based photopolymer that is cured by a UV laser after each layer is placed. As a result, Jetted Photopolymer is also known as Photopolymer Inkjet Printing. The benefits of this method include very high precision and surface finishes. However, feature quality and material characteristics are not as excellent as in Stereolithography.
Jetted photopolymer Material – Objet Geometries Ltd. V.S 3D Systems
Both Objet Geometries Ltd. and 3D Systems developed equipment deposits the photopolymer build material as stated above, but varies in the application of support material. In the year 2000, Objet, an Israeli business, launched its PolyJet technology. The support material in the PolyJet system is likewise a photopolymer that is deposited from a second print head and cured by UV light. This support material does not cure as quickly as the construction material and may be removed with pressured water. In 2003, 3D Systems marketed its InVision systems. A second print head is used in these jetted photopolymer devices to deposit a wax support material. When the portion is finished, the wax is melted away.
Objet Geometries Ltd. and 3D Systems are two businesses that have created jetted photopolymer devices. Object Geometries created the first Jetted Photopolymer 3D printer in 2000. Quadra was the name of the printer. Photopolymer printers with jetted heads typically feature two or more jetting heads. One head jets the construct material, while the other heads jet the support material. Multi-material and multi-color items may be printed using printers with numerous print heads. Above the build plate, the print heads move in the X-Y directions. When printing, small droplets of UV reactive photopolymer are jetted onto the build plate. A UV light situated adjacent to the print head rapidly solidifies these drips. For the following layer to be printed, the build plate travels down by an increment. A single layer’s thickness is typically between 14 and 28 microns, allowing for a high degree of detail.

Applications
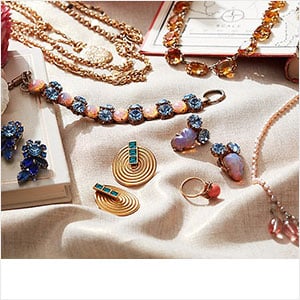
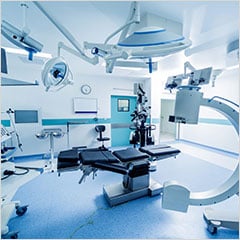
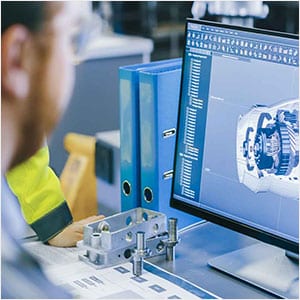
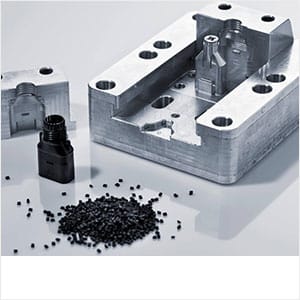
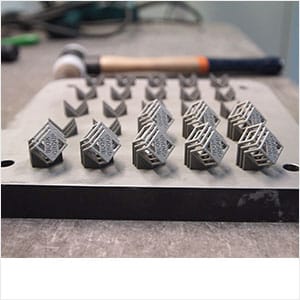
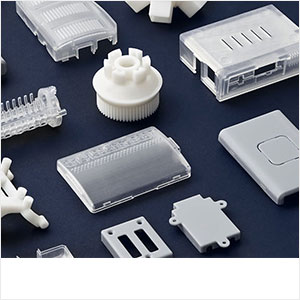
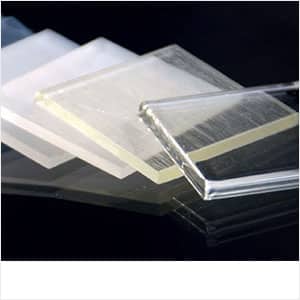
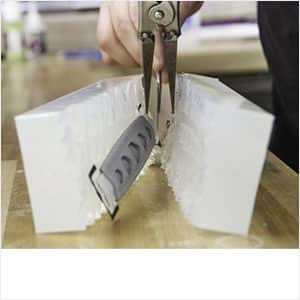
Jetted Photopolymer Support Structures
There are typically two kinds of support options available with Polyjet printers: matte and glossy. Matte supports entirely encase the printed product in the backing material. These are utilized on the majority of prints and are suggested for the greatest dimensional accuracy.
Supports are generated only beneath overhangs and “floating” portions when the glossiness option is used. The printed model has a glossy appearance in the parts where there are no supports. Glossy supports may significantly cut print time and resource usage (on some prints). There will usually be visible variations between regions printed with and without supports; the portions covered with supports will be matte. Wax is the most common support material used in 3D Systems printers (MultiJet). By putting the 3D printed object in a tiny oven or a hot oil bath, these supports are melted away. In the majority of their new machines, Stratasys (PolyJet) use water-soluble supports. The 3D printed sculpture is immersed in water to dissolve the soap-like supports. In earlier machines, a gelatin-like substance is used to print the supports, which must be removed manually or by water blasting.
Jetted Photopolymer Capabilities | |
---|---|
Abbreviation | JP |
Build Speed | Fast |
Surface Finish | Smooth |
Tolerance | 0.001 in. |
Min Feature Size | 0.006 in. |
Min Layer Thickness | 0.0006 in. |
Max Part Size | 19.30 x 15.40 x 7.90 in. |