Processes
- Polymer Processing
- Injection Molding Insert Molding Blow Molding Over Molding Metal Injection Molding Thermoforming
- Metal Casting
- Die Casting Castings & Forgings Wax Casting Lost Wax Casting Grey Iron Castings Centrifugal Casting Investment Casting Permanent Mold Sand Casting Shell Mold Casting Aluminum Investment Casting Brass Investment Casting Steel Investment Castings Titanium Investment Casting
- Machining
- Milling Turning EDM machining CNC Engraving Hole-making Tap Size Chart Drill Size Chart 5 axis machining Micro Machining CNC Cutting Metal Processes Ceramic Manufacturing Swiss Precision Machining
Materials
Shell mold casting is a casting method to produce castings with thin shell mold, also it’s ideal for medium-to-high-volume production. Similar to the sand casting, in that molten metal, a dispensable mold is poured. Shell casting was invented by German J. Cronin in 1943. It was first used in Germany in 1944 and began to be used in other countries after 1947.
What Are The Working Steps In Shell Moulding Process?
A kind of heat hardening molding sand (phenolic resin coated sand) is used to cover the metal template heated to 180-280 ℃ to harden it into a thin shell (the thickness of the shell is generally 6-12mm), and then the shell is heated and solidified to achieve sufficient strength and rigidity. Therefore, the upper and lower shell can be clamped with clamps or bonded with resin, and the mold can be formed without sand box, The heating temperature of casting metal template is about 300 ℃, and the molding sand used is resin sand, that is, resin sand with phenolic resin as binder. Similarly, the core can be made into thin shell by the above method, and the tipping bucket method is commonly used to make the thin shell mold. The blowing method is commonly used in the manufacture of thin shell core.
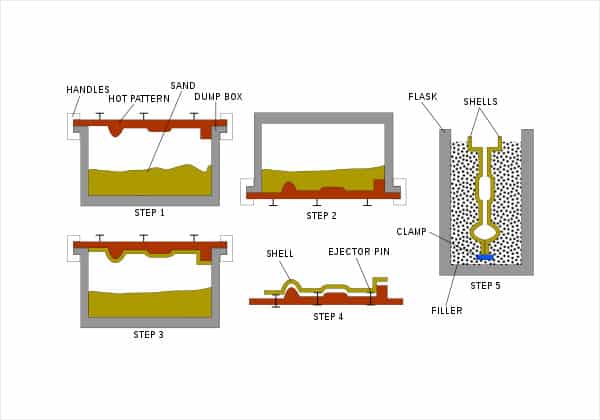
What Are The Advantages Of Shell Mold Casting
- Shell molding may be completely automated for large manufacturing.
- High productivity, reduced labor costs, outstanding surface finishes and technique accuracy may pay more than their own if machining costs are reduced.
- The absence of moisture in the shell means that there are minimal problems due to oxygen, and that little gas still present may escape rapidly through the brittle shell. Some resin binder peels out on the surface of the shell when the metal is washed.
- The finishing of the surface is extremely good, the production rate is high, labor costs cheap, complicated shapes and fine details may be produced.
- A tiny scrap was generated by low tooling costs.
- Very large components and complex shapes may be produced.
- Low cost of tools and equipment.
- Scrap recycling is feasible.
- Short lead time is possible.
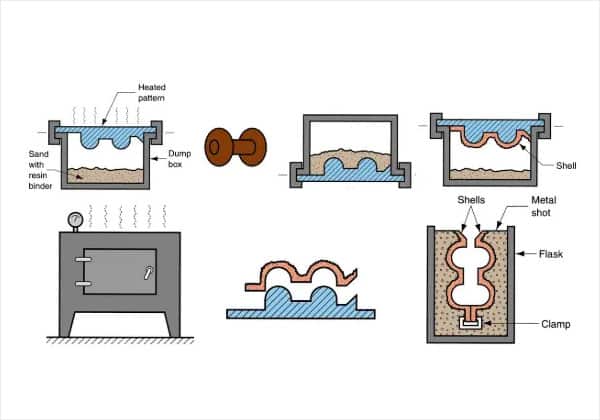
What Are The Disadvantages Of Shell Mold Casting
- The gating mechanism must be part of the pattern since the whole mold consists of a costly pattern.
- The resin for the sand is costly, but not much is needed, since just a shell is produced.
- High cost of equipment.
- Poor strength of material.
- High potential porosity.
- Secondary machining is frequently necessary.
- High physical labor costs.
Applications Of Shell Mold Casting
Modern shell mold provides flexibility. Many industries make significant use of this type of production. Companies now use shell casting to produce cylinders, valve bodies, rods, cam shafts, arms with levers, coils, and gearboxes. In manufacturing, shell molding and casting play a significant role from automotive and consumer products to industrial manufacture.
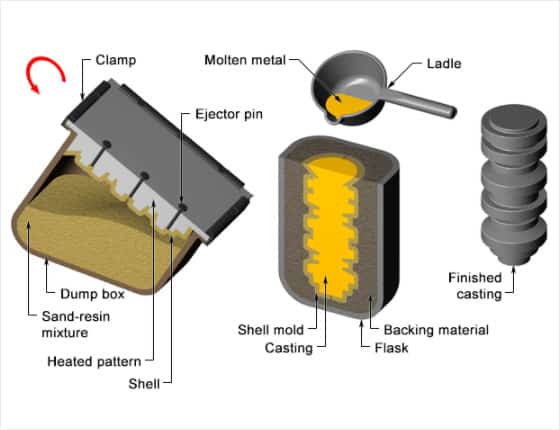
What Is The Difference Between Sand Mold And Shell Mold Casting?
Shell molds and sand molds utilize sand both as mold material, but in different ways. Sand mold casting form sand cavities and pour the molten metal into the cavity. While shell molds make a pattern, put the patter in a sand/binding mix box. The sand/binding unit is put on the motif and produces a sand mould over the pattern, which removes the mould from the pattern and pours the molten metal in the mould.
Both shells and sand molds utilize sand but in distinct ways in which sand mold produces a hollow inside a flask of sand. While molding the shell is using sand combined with a bonding resin to cover a heated pattern in order to produce a mold.