Processes
- Polymer Processing
- Injection Molding Insert Molding Blow Molding Over Molding Metal Injection Molding Thermoforming
- Metal Casting
- Die Casting Castings & Forgings Wax Casting Lost Wax Casting Grey Iron Castings Centrifugal Casting Investment Casting Permanent Mold Sand Casting Shell Mold Casting Aluminum Investment Casting Brass Investment Casting Steel Investment Castings Titanium Investment Casting
- Machining
- Milling Turning EDM machining CNC Engraving Hole-making Tap Size Chart Drill Size Chart 5 axis machining Micro Machining CNC Cutting Metal Processes Ceramic Manufacturing Swiss Precision Machining
Materials
What does CNC stand for? CNC stands for Computerized Numerical Control. The so-called numerical control cutting refers to the workpiece instruction (or program) used to control the machine tool or equipment. It is a new control mode given in the digital form. When the command is provided to the control device of CNC automatic metal cutting machine, the cutting machine can cut automatically according to the given program. Numerical control cutting technology is the organic combination of traditional processing technology and computer numerical control technology, computer aided design and aided manufacturing technology. CNC cutting is composed of CNC system and mechanical framework. Compared with the traditional manual and semi-automatic cutting, CNC cutting can effectively control and improve the cutting quality and efficiency through the cutting technology, cutting process and automatic control technology provided by the CNC system controller.
How Does A CNC Cut?
Usually, the CNC metal cutting system automatically processes the parts to be processed according to the pre programmed processing program (commonly used drawing software AutoCAD). According to the instruction code and program format specified by the CNC cutting system, we compile the machining process route, process parameters, tool trajectory, displacement, cutting parameters (spindle revolution, feed rate, back feed, etc.) and auxiliary functions (tool change, spindle forward rotation, reverse rotation, cutting fluid on and off, etc.) of the parts into the machining program sheet, Then the contents of the program list are recorded on the control medium (such as perforated paper tape, magnetic tape, magnetic disk, magnetic bubble memory), and then input into the numerical control device of the numerical control machine tool, so as to command the machine tool to process parts.

Advantages of CNC Cutting
Through computer drawing, parts optimization nesting and CNC programming, the CNC nesting software effectively improves the utilization rate of steel and the work efficiency of cutting production preparation. The Metal CNC cutting machine can effectively control and improve the cutting quality and efficiency through the cutting technology, cutting process and automatic control technology provided by the CNC system controller.
Disadvantages Of CNC Cutting
Due to higher cutting efficiency and more complex nesting programming, if the optimized nesting programming software is not used or used well, the steel waste will be more serious, resulting in faster cutting, more cutting and more waste. A numerical control system, or controller, is the heart of a numerical control cutting machine. If an advanced CNC system is not used, or the CNC system does not have the cutting process and cutting experience, it will lead to cutting quality problems, thereby cutting efficiency and resulting in waste of steel.
Applications Of CNC Cutting
The CNC router may be used in the manufacture of products such as door sculptures, interior and exterior decorations, wood panels, sign boards, wooden frames, mouldings, musical instruments and mobilizers. They are also used in the industry in plastics thermoforming by automating the cutting process. CNC routers can provide component reproducibility and adequate manufacturing efficiency or enable the creation of one-off designs. This is engraving machine.
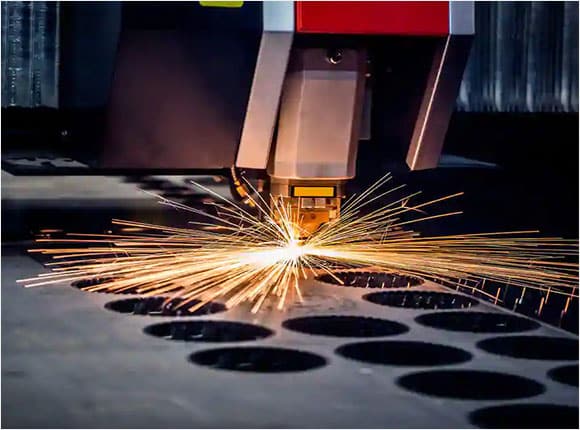
CNC Cutting Machine Types
Basically, five main kinds of CNC machines are utilized and the CNC cutting tools are depending on the machine type, nature of the project, and overall accuracy of the project. The five wide CNC machinery types are:
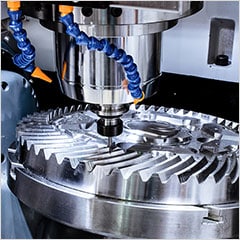
CNC Milling Machine
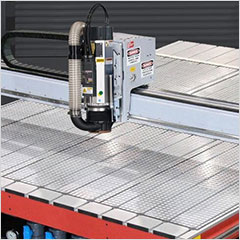
CNC Routers
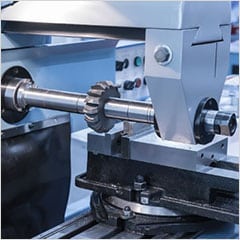
CNC Lathes
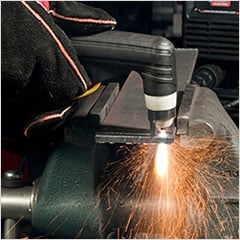
Plasma Cutters
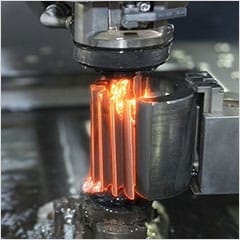