Processes
- Polymer Processing
- Injection Molding Insert Molding Blow Molding Over Molding Metal Injection Molding Thermoforming
- Metal Casting
- Die Casting Castings & Forgings Wax Casting Lost Wax Casting Grey Iron Castings Centrifugal Casting Investment Casting Permanent Mold Sand Casting Shell Mold Casting Aluminum Investment Casting Brass Investment Casting Steel Investment Castings Titanium Investment Casting
- Machining
- Milling Turning EDM machining CNC Engraving Hole-making Tap Size Chart Drill Size Chart 5 axis machining Micro Machining CNC Cutting Metal Processes Ceramic Manufacturing Swiss Precision Machining
Materials
Aluminum Investment Casting – What Is Aluminum Investment Casting?
Aluminum investment casting is a technique that creates industrial components by metallically reproducing wax models. Molten aluminum is used to produce components with a very smooth surface finish, excellent dimensional accuracy, and sharp detail that is free of flash or parting lines. Aluminum Investment Castings allows the casting of complex-geometry components faster, with more alloy flexibility, tighter dimensional tolerances, and superior surface finishes, resulting in near-net-shape products that need less machining and other processing than conventional casting methods. Aluminum investment castings are used extensively in a wide variety of industries and applications. Aluminum parts and components are used in a variety of industries, including medical and dental equipment, food and dairy, aerospace, military, and electronics.
The Aluminum Investment Casting Process – How Does Aluminum Investment Casting Work?
The procedure starts with the carving or injection molding of a wax design called the master die. The wax pattern may be combined with other wax patterns and then connected to a wax sprue or rod to allow for simultaneous casting. Around the sprue, many hundred designs may be constructed. Once securely connected, a ceramic slurry referred to as the investment is administered in one of two ways. The initial step involves repeatedly dipping the cluster of designs into the investment and removing it to create a consistent surface and thickness. The alternative technique is to put the cluster in a flask and fill it with the investment, shaking the flask to enable trapped air to escape and to ensure that all the gaps within are completely filled with the investment. The assembly is next dried, which may be expedited by putting it in a vacuum or using a fan. Once completely dry, the assembly is inverted and put in a furnace or oven. The wax melts and either drip or vaporizes. The mold is next heated to eliminate any remaining moisture or wax; this procedure is referred to as burnout. Liquid aluminum is poured into the area formerly occupied by wax and is pulled in using gravity, vacuum, positive air pressure, or centrifugal casting techniques. After cooling, the hardened investment shell is pounded, vibrated, dissolved, or sand or water-blasted away, exposing the aluminum component inside.
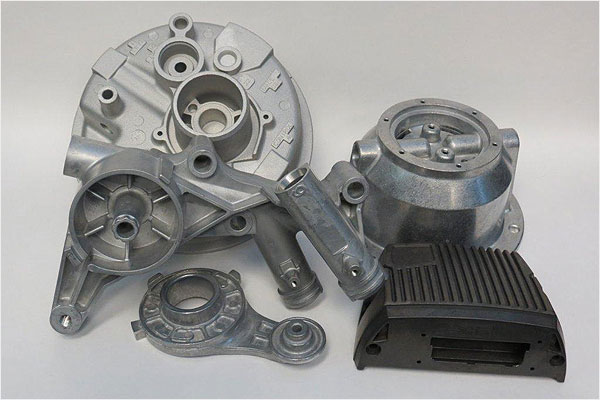
Aluminum Investment Casting Applications
Aluminum investment castings are used extensively in a wide variety of industries and applications. Aluminum parts and components are used in a variety of industries, including medical and dental equipment, food and dairy, aerospace, military, and electronics. Typical examples of aluminum casted parts include Valves, Pistol Frames, Medical Devices, Heat Sinks, and Levers.
Aluminum investment casting enables the production of complex-geometry parts with shorter lead times, increased alloy flexibility, tighter dimensional tolerances, and improved surface finishes, resulting in near-net-shape parts that require less machining and other processing than other casting processes.
Advantages of Aluminum Investment Casting
- Aluminum Investment Castings enables the creation of intricate patterns and shapes. This enables producers to quickly obtain bespoke castings that meet their specific manufacturing requirements.
- Aluminum investment castings enable manufacturers to create components at a much greater and quicker pace than with other alloy materials. Aluminum dies casting may also reach the near-net form, which eliminates the need for machining to create completed components.
- Aluminum investment castings are as strong as steel but are much lighter. Aluminum components also have a better look and aesthetic value when compared to other metal alloys. However, since aluminum die-cast components are less expensive, end customers may get high-quality metal goods at a low price.
- Aluminum castings are adaptable, corrosion-resistant, and may be utilized for a variety of applications. These characteristics enable manufacturers to create a variety of products utilizing aluminum components. Additionally, the final goods have a longer useful life, providing customers with a greater value for their money.
- The flexibility of quantity. Regardless of the amount, it may be created at any moment.
- Thermal conductivity and heat dissipation are excellent. As a result, it is extensively used in radiator devices.
- Aluminum castings are lightweight and have a low specific gravity. As a result, it is very popular in sectors that demand lightweight construction, such as cars, trains, and aircraft.
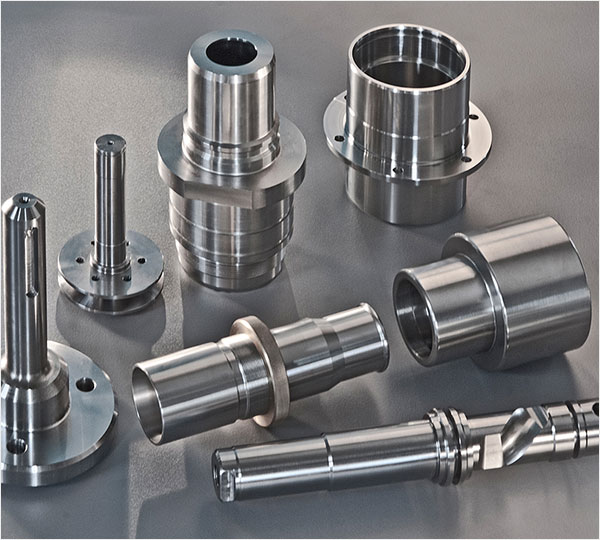
Aluminum investment castings are extensively utilized due to all the benefits listed above. Particularly in the mechanical equipment, automotive, mining machinery industries, the aerospace industry, and so on.