Processes
- Polymer Processing
- Injection Molding Insert Molding Blow Molding Over Molding Metal Injection Molding Thermoforming
- Metal Casting
- Die Casting Castings & Forgings Wax Casting Lost Wax Casting Grey Iron Castings Centrifugal Casting Investment Casting Permanent Mold Sand Casting Shell Mold Casting Aluminum Investment Casting Brass Investment Casting Steel Investment Castings Titanium Investment Casting
- Machining
- Milling Turning EDM machining CNC Engraving Hole-making Tap Size Chart Drill Size Chart 5 axis machining Micro Machining CNC Cutting Metal Processes Ceramic Manufacturing Swiss Precision Machining
Materials
Among the various casting processes definitively introduced into industrial practice, the die casting method is certainly the one that is called, at least for parts in large series of non-ferrous alloys, to the widest development.
The large number of parts that it is able to supply and their low cost, together with the possibility of reducing subsequent machining to a minimum, has decidedly oriented the construction technique in this sense, which uses this method every time The problem arises of producing, at a low price, a large series of parts, from which important mechanical and aesthetic characteristics are required.
What Is Die Casting?
Die casting is a manufacturing process that uses high pressures to force molten metal from a crucible into a metal jacket. Subsequently, the material is injected through a stem into a preformed mold (matrix). Once injected, the piece cools, solidifies and is removed from the mold. This process is used for both pieces and ingots.
Sometimes post-casting treatments are necessary, depending on the process and the metal used: roughing, surface cleaning, heat treatments, machining, etc.
The manufactured parts are characterized by their great uniformity, good surface finish and great dimensional precision. The dimensions of the parts vary depending on the specifications. Weights range from a few grams for the smallest pieces to several tons. We can even get extremely thin-walled parts. In fact, most parts do not need the final machining process or require very light machining.
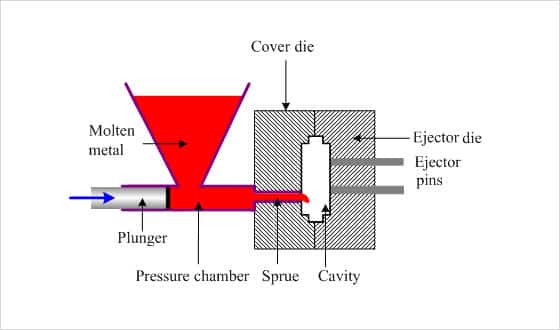
Die Casting Process – How Does Die Casting Work Exactly?
The halves of the die casting mold are each mounted on a fixed and a movable machine plate of the die casting machine. Because of the high pressure during casting, locks with large locking forces are required to hold the die casting mold together. The mold halves are sprayed with a release agent before they are closed so that the finished casting can later easily be released from the mold and the plates do not get too hot over time. Up to this point the procedure is always the same. However, we now have to differentiate between two different types of die casting machines: the hot chamber and the cold chamber die casting machine.
Machines are needed for die casting; These, although they are all based on the principle common to this casting procedure, consisting of the violent introduction of a certain amount of molten or pasty metal into a permanent mold, by means of a pressure exerted from the outside, are extremely varied; but modern technique has been oriented towards a few types that are classified as follows:
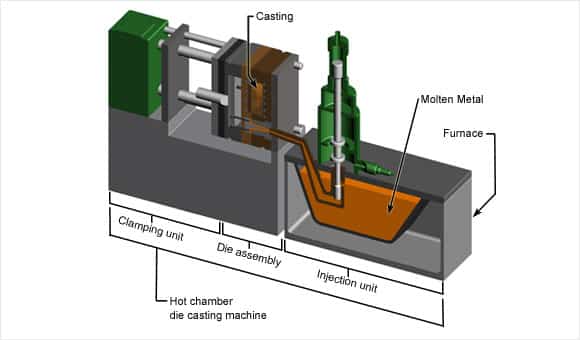
a) Hot chamber die casting process – Machines with hot pressure chamber, or for injected cast iron.
In the case of the hot chamber die casting machine, the “casting set” (that is, the piston that shoots the metal into the mold and the tube surrounding it) is located in the liquid metal. These machines are mainly used with metals with a low melting point such as zinc and magnesium alloys.
b) Cold chamber die casting process – Machines with cold pressure chamber, or for die casting.
The cold chamber die casting machines are mainly used for aluminum alloys, as these have a relatively high melting point. The casting set is located here – who would have thought it – outside of the melt.
The subsequent processes are then the same for both machines. Because when the metal has solidified, the two halves of the mold open and the casting is automatically pushed out of the mold with the help of ejector pins. The casting is then taken over by an industrial robot. This removes the sprue system and any remaining burrs. Finished!
Die Casting Tolerances – Depending on Various Factors
In the die casting process, the tolerances result from the alloys, the casting molds and the casting process. The dimensional deviations of die-cast parts made of light metal alloys are mainly dependent on the functional and dimensional accuracy of the steel mold, the position of the mold division and the shape of the cast part. In this way, tolerances of ± 0.17 and ± 1 are possible.
Which Materials Can Be Used for Die Casting?
Possible materials for this procedure – Aluminum, zinc, silicon tombac, and magnesium are the most commonly used die casting alloys. Their mechanical properties differ so widely that they can be used for almost any purpose. In addition, they are completely recyclable, corrosion-resistant, thermally conductive, electrically conductive and have excellent EMI / RFI shielding as well as good further processing properties.
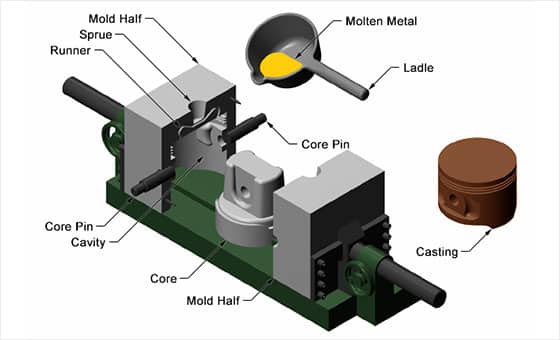
Aluminum Die Casting
Aluminum die-casting is a die-casting process in which aluminum in the pasty or liquid state is pressed under high pressure into a steel mold that has been preheated. The steel mold consists of two halves, so that the mold can be easily opened after the filling process and the solidification of the metal and the casting can be removed. Aluminum die casting is basically only produced on cold chamber die casting machines. The term “aluminum die-cast” is not entirely correct, as pure aluminum is seldom used as a cast material due to its strength properties. It was only through its alloys that aluminum achieved technical importance. These include AlSi9Cu3 (Fe), AlSi12Cu1 (Fe), AlSi12 (Fe) and AlSi10Mg (Cu). They significantly improve the casting and strength properties of aluminum. Hypereutectic and hypereutectic Al-Si alloys and alloys with hot and cold aging are also being cast with increasing frequency.
Steel Die Casting
Steel is used in die casting as the material for the casting molds. High-strength hot-work steels such as 32CrMoV 12-28, X37CrMoV 5-1 or X40CrMoV 5-1 according to DIN EN ISO 4957 are used for this.
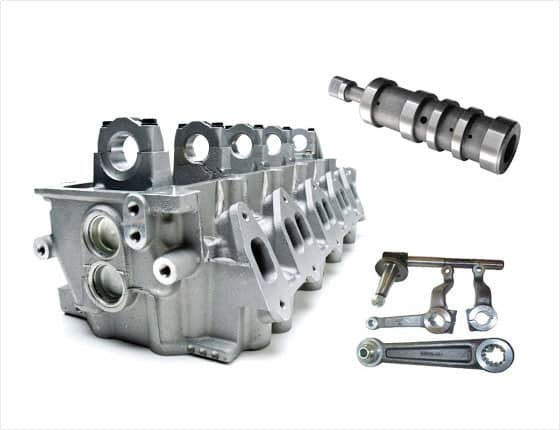
Advantages of Die Casting
- Very short production cycles.
- Suitable for thin-walled, complex component geometries
- High mechanical properties in combination with low weight.
- Parts with good properties for subsequent machining.
- Excellent dimensional stability, parts can be produced with tight dimensional tolerances.
- Excellent surface finish and edges.
- Economically, large quantities possible
Disadvantage of Die Casting
- Cost-intensive steel tools (permanent molds) only economical for large quantities
- Only suitable for cast parts without undercuts
- Only partially weldable
- Poorer corrosion properties
- Higher weight
- More complex production
- Complicated geometries not possible in some cases
- Mechanical and thermal stress on the expensive steel molds
- Porous structure due to inclusions of air possible if no special measures are taken to vent the mold -> low strength values
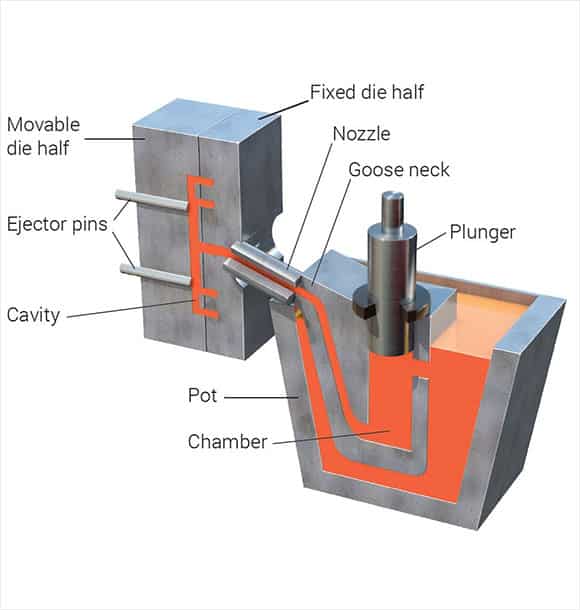
Flexible Application of Die-Cast Parts
Die-cast parts are used in many branches of industry for covers, fittings, housings or fittings. Depending on the requirements, die-cast parts can also be provided with improved corrosion protection or higher wear resistance. In addition, depending on the aftertreatment and alloy, die-cast parts with different surfaces such as brushing, chromating, wet painting, tumbling, anodizing, pad printing, screen printing, copper plating or nickel plating are possible. Common die-cast parts are aluminum die-cast, magnesium die-cast and zinc die-cast.