Processes
- Polymer Processing
- Injection Molding Insert Molding Blow Molding Over Molding Metal Injection Molding Thermoforming
- Metal Casting
- Die Casting Castings & Forgings Wax Casting Lost Wax Casting Grey Iron Castings Centrifugal Casting Investment Casting Permanent Mold Sand Casting Shell Mold Casting Aluminum Investment Casting Brass Investment Casting Steel Investment Castings Titanium Investment Casting
- Machining
- Milling Turning EDM machining CNC Engraving Hole-making Tap Size Chart Drill Size Chart 5 axis machining Micro Machining CNC Cutting Metal Processes Ceramic Manufacturing Swiss Precision Machining
Materials
What Is Additive Fabrication (AF)
Additive fabrication (AF) covers a series of technologies. These technologies use the method of building parts layer by layer to gradually construct solid parts from virtual three-dimensional models. The traditional material reduction fabrication process is to remove all unnecessary materials from a piece of material (by manual engraving, or using equipment such as milling machine, lathe or CNC machine tool) until the required parts are obtained.
The Process Of Additive Fabrication
There are different methods to perform Additive fabrication processes. An increasingly popular method is 3D printing. Compared with the material reduction fabrication process, the material addition fabrication starts from scratch, and the parts are constructed by “printing” a new layer on the top of the previous layer until the parts are completed. The thickness of each layer varies from a few microns to about 0.25mm according to the specific additive fabrication technology used. At present, many materials can be applied to different additive fabrication processes.
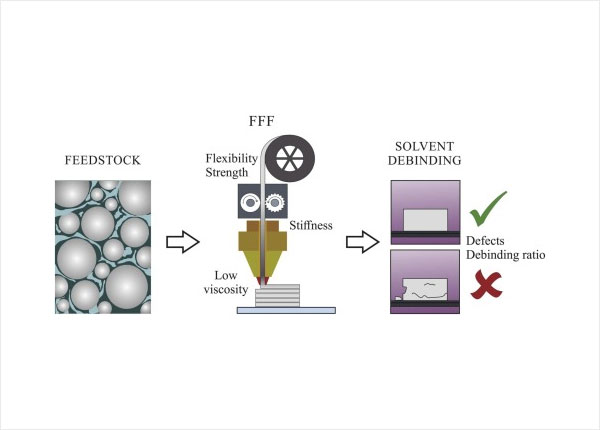
The Advantage Additive Fabrication Process
The main advantage of additive manufacturing is that it can create geometrically complex shapes without wasting excess materials. Another advantage of this process is that it does not require many tools and is a very cost-effective manufacturing process. The additive fabrication process has different embodiments, and the increasingly popular method is 3D printing. This type of fabrication is energy-saving and environmentally friendly. The materials used, especially 3D printing, eventually create lightweight designs for some end products. With the use of additive fabrication, physical tools are reduced and attention is increased. The spatial design program allows engineers to have greater freedom in thinking to design and create some products without being limited by traditional machining. This technology can also reduce the individual parts of the whole product.
The History Of Additive Fabrication
The historical basis of additive fabrication (AF) can be traced back to almost 150 years ago when people used two-dimensional layer superposition to form a three-dimensional topographic map. The research work in the 1960s and 1970s verified the first batch of modern am processes, including photopolymerization technology in the late 1960s, powder melting process in 1972, and sheet lamination technology in 1979. By the 1980s and early 1990s, the number of am-related patents and academic publications had increased significantly, and many innovative am technologies appeared, such as 3D printing technology (3DP) of MIT in 1989 and the laser beam melting process in the 1990s. During the same period, some am technologies were successfully commercialized, including light curing (SL), solid melt deposition (FDM), and laser sintering (SLS). The 1990s and 2000s were the growth period of being. In the late 2000s, metal is technology stood out among many am technologies and became the focus of market attention.
Additive Fabrication Process Chain
All additive fabrication starts from creating a virtual 3D CAD model, which can be completed by almost any 3D computer-aided design (CAD) software. However, the CAD model used for additive fabrication must be in the form of a completely closed “watertight” volume (for example, a cube model must contain all six faces and there is no gap at the joint). If one of the faces of the model is missing or has gaps, it is indicated as an infinitely thin surface, which cannot be printed (however, the model can be automatically repaired with some am software according to the severity of the error).
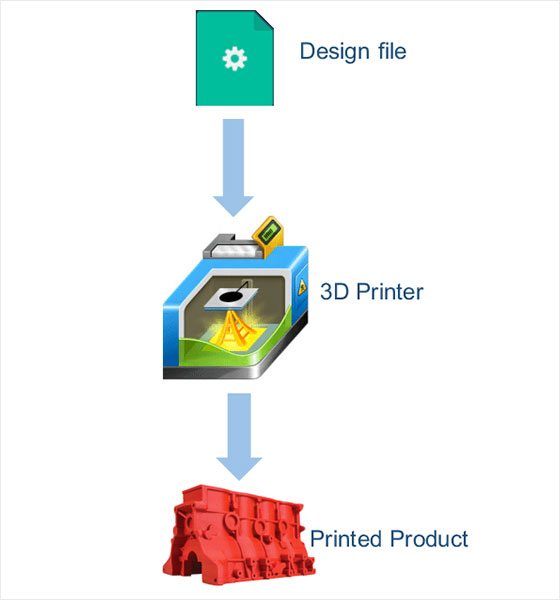