Processes
- Polymer Processing
- Injection Molding Insert Molding Blow Molding Over Molding Metal Injection Molding Thermoforming
- Metal Casting
- Die Casting Castings & Forgings Wax Casting Lost Wax Casting Grey Iron Castings Centrifugal Casting Investment Casting Permanent Mold Sand Casting Shell Mold Casting Aluminum Investment Casting Brass Investment Casting Steel Investment Castings Titanium Investment Casting
- Machining
- Milling Turning EDM machining CNC Engraving Hole-making Tap Size Chart Drill Size Chart 5 axis machining Micro Machining CNC Cutting Metal Processes Ceramic Manufacturing Swiss Precision Machining
Materials
What Is Metal Injection Molding (MIM)
Metal injection molding (MIM) is a new kind of powder metallurgy near net forming technology, which is derived from the plastic injection molding industry. As we all know, MIM can produce various complex shaped products with low price, but the strength of plastic products is not high, Metal or ceramic powder can be added into plastics to obtain products with high strength and good wear resistance.
In recent years, the idea has evolved to maximize the content of solid particles and completely remove the binder and densify the preform during the subsequent sintering process. This new powder metallurgy forming method is called metal injection molding. Using a standard injection molding machine, the powder is melted and injected into a mold, where it cools and solidifies into the shape of the desired part. Subsequent heating processes remove the unwanted polymer and produce a high-density metal part.
Metals commonly used for MIM parts include the following:
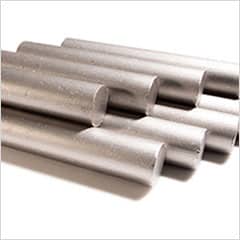
Low alloy steels
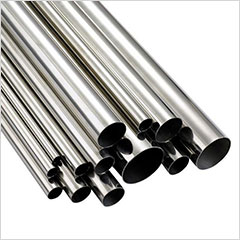
Stainless steels
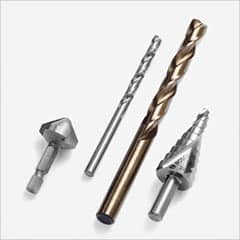
High-speed steels
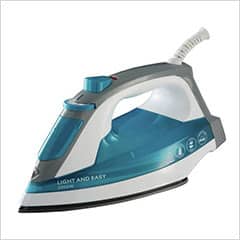
Irons
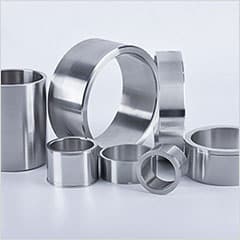
Cobalt alloys
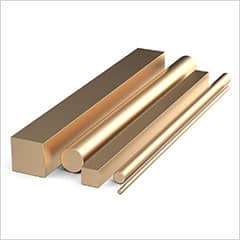
Copper alloys
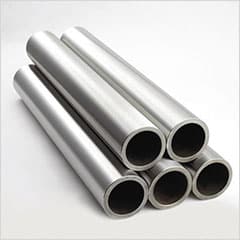
Nickel alloys
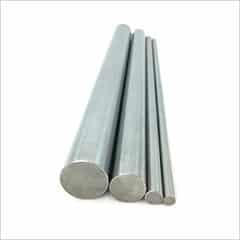
Tungsten alloys
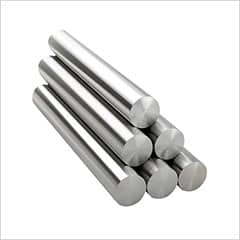
Titanium alloys
MIM manufacturing process generally includes mixing granulation, injection molding, degreasing, sintering and secondary treatment. Combined with the flexibility of injection molding design and the high strength and integrity of precision metal, it is suitable for mass production of small, precision, complex shape and metal and ceramic parts with special performance requirements, and has broad application prospects and economic value.
- Mixing: Fine metal powder is mixed with thermoplastic and paraffin binder in precise proportion. It is mixed in special mixing equipment and heated to a certain temperature to melt the binder. In most cases, mechanical mixing is used until the metal powder particles are evenly coated with the binder and cooled to form granular raw materials.
- Injection molding: Injection molding equipment and technology are similar to injection molding. The raw material is heated by the machine and injected into the cavity under high pressure. This link forms (green part) after cooling demoulding, only in about 200 ° The whole process can be carried out only when the binder is melted (fully fused with the metal powder) under the condition of C. The shrinkage of metal parts during sintering should be considered in cavity size design.
- Debinding: The use of physical or chemical methods to remove the binder in parts, the most commonly used is solvent extraction. Most of the binder is removed before sintering, and the residual part can support the parts to enter the sintering furnace, which is volatilized during sintering. The part is changed from the mixture of metal powder and binder into a pure metal part, the volume shrinks and the shape and structure remain unchanged.
- Sintering: The parts are put into a furnace controlled by high temperature and high pressure. The part is slowly heated under the protection of gas to remove the residual adhesive. After that, the part will be heated to a high temperature, and the gap between particles will disappear due to the fusion of particles. The part shrinks directionally to its design size and transforms into a compact solid, the volume shrinks further, and the shape and structure remain unchanged.
- Surface treatment: Common surface treatment processes of MIM parts include polishing, electroplating, PVD, blackening, phosphating, spraying, etc.
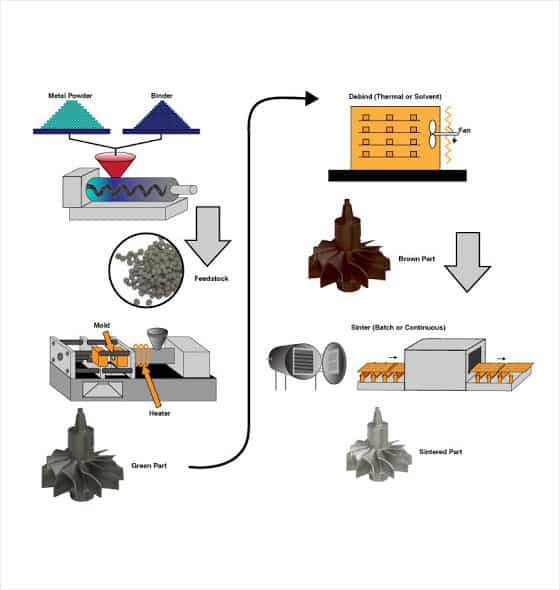
MIM Design Rules
When designing parts to be manufactured using metal injection molding, most of the design rules for plastic injection molding still apply. However, there are some exceptions or additions, such as the following:
- Wall thickness: Similar to plastic injection molding, wall thickness should be kept to a minimum and consistent throughout the part. It’s worth mentioning that reducing wall thickness in the MIM process reduces not only material volume and cycle time, but also debinding and sintering periods.
- Draft: Many MIM parts do not require any draft, unlike plastic injection molding. Most injection molded polymers are more difficult to remove from the mold than the polymer binder used in the powder material. Also, because the metal powder in the mixture takes longer to cool, MIM pieces are evacuated before they have fully cooled and shrunk around the mold features.
- Sintering support: MIM parts must be adequately supported during sintering or they will twist as they shrink. Standard flat support trays can be used if parts are designed with flat surfaces on the same plane. Custom supports, which are more expensive, may be required if this is not the case.
Features Of Metal Injection Molding
- It has high degree of freedom in geometry, and can produce metal parts with complex shape by one-step forming, just like plastic products, with uniform density and high dimensional accuracy. It is suitable for manufacturing small parts (0.05g-200g) with complex geometry, precision and special requirements.
- The alloy has good flexibility, and the manufacturing cost can be reduced for the parts with segregation or pollution during casting of hard, brittle and difficult to cut materials or raw materials;
- The product has stable quality and reliable performance. The relative density and width of the product can reach 92-98%. The product has high mechanical properties such as strength, hardness and elongation, good wear resistance, fatigue resistance and uniform structure. It can be carburized, Quenched and tempered;
- The product has low cost, good finish and high precision( ± 0.3%~ ± 1%), typical tolerance is ± 05mm, generally without subsequent processing;
- High utilization rate of raw materials, high production efficiency, high degree of production automation, simple process, continuous large-scale production.
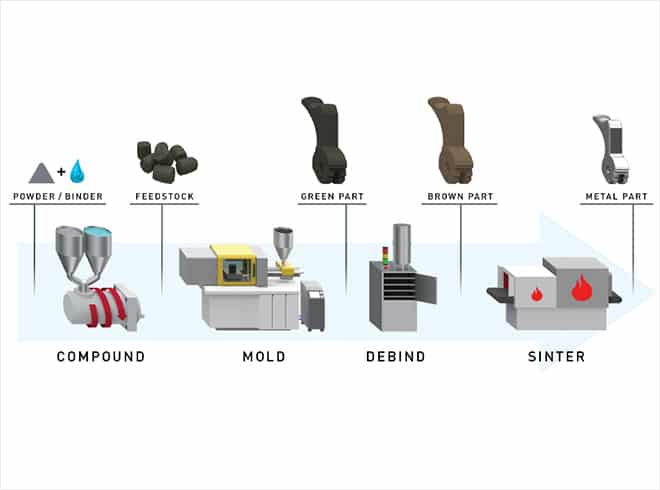
Applications Of Metal Injection Molding
- Automobile parts: airbag parts, automobile lock parts, safety belt parts, automobile door lifting system, pinion, small parts of automobile air conditioning system, rack in brake system, small parts of sensor in fuel supply system.
- Military parts: gun parts, ammunition parts, credit parts.
- Computer and it industry: such as mobile phone holder, mobile phone structural parts, printer parts, magnetic core, striker pin, drive parts, optical communication ceramic plug.
- Tools: such as drill, cutter head, nozzle, spiral milling cutter, pneumatic tools, fishing gear parts, etc.
- Household appliances: such as watch case, watch chain, electric toothbrush, scissors, golf head, jewelry chain, cutting tool head, etc.
- Medical machinery parts: such as orthodontic frame, scissors, tweezers.
- Electrical parts: micro motor, sensor parts.
- Mechanical parts: such as textile machine, crimping machine, office machinery parts, etc.
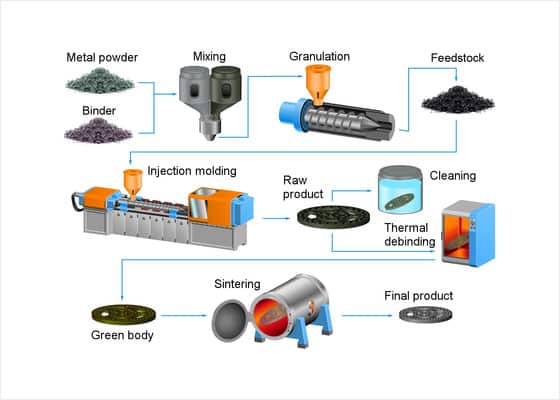
Metal Injection Molding Capabilities | ||
---|---|---|
Typical | Feasible | |
Shapes: | Thin-walled: Cylindrical Thin-walled: Cubic Thin-walled: Complex |
Flat |
Part size: | Weight: Typically < 9 oz. | |
Materials: | Metals Titanium Alloy Steel Cast Iron Carbon Steel Stainless Steel Copper |
Ceramics Composites |
Max wall thickness: | 0.04 – 0.25 in. | 0.01 – 1.2 in. |
Advantages: | Can form complex shapes and fine details Good surface finish Good mechanical properties Productivity is high |
|
Disadvantages: | Limited part size Thin-walled parts only Tools and equipment cost a lot | |
Applications: | Metal parts in surgical instruments, electronic products and consumer goods |