Processes
- Polymer Processing
- Injection Molding Insert Molding Blow Molding Over Molding Metal Injection Molding Thermoforming
- Metal Casting
- Die Casting Castings & Forgings Wax Casting Lost Wax Casting Grey Iron Castings Centrifugal Casting Investment Casting Permanent Mold Sand Casting Shell Mold Casting Aluminum Investment Casting Brass Investment Casting Steel Investment Castings Titanium Investment Casting
- Machining
- Milling Turning EDM machining CNC Engraving Hole-making Tap Size Chart Drill Size Chart 5 axis machining Micro Machining CNC Cutting Metal Processes Ceramic Manufacturing Swiss Precision Machining
Materials
What is Micro Machining?
Micro machining, also known as micromachining, is a manufacturing process of creating very small parts using mechanical micro tools with geometrically defined cutting edges to make the subtractive fabrication of products or features with at least some dimensions within the micrometer range. The tools used for micro machining may be as small as 0.001 inch in diameter. The traditional machining methods are typical turning, milling, creating, casting, etc., with the birth and development of integrated circuits, a new technology, micromachining technology, has appeared and developed as a technique in the late 1990s. In micromachining, particles or rays with a certain energy, such as electron beam, ion beam, and light beam, are often used to interact with the solid surface to produce physical and chemical changes, so as to achieve the desired purpose. Micromachining can create intricate parts in small sizes for certain applications, particularly in the semiconductor and medical industry.
Classification of Micro Machining – Techniques & Types of Micro Machining Processes
Many processes of micromachining are carried out in a vacuum, such as evaporation, sputtering, deposition, vapor phase epitaxy, plasma, and reactive ion etching. These processes play an important role in micromachining. Many of these processes are physical processes, and some processes involve chemical processes. Micromachining techniques can be divided into the physical process, chemical process and mechanical process according to the physical properties of the removal process. Although physical and chemical processes are confined to specific applications, mechanical is nearly ubiquitous. This is because a vast range of engineering materials, such as metals and polymers, may be treated, and diverse surfaces with distinct functionalities can be produced.
1.Physical Micro Machining
- Laser beam machining: a form of machining process uses thermal energy directed from a laser beam to remove material from metallic or nonmetallic surfaces, best suited for brittle materials with low conductivity but can be used on most materials.
- Ion beam machining: an important unconventional manufacturing technology for micro/nanomanufacturing. It uses accelerated ion current in a vacuum chamber to remove, add or modify atoms on the surface of objects.
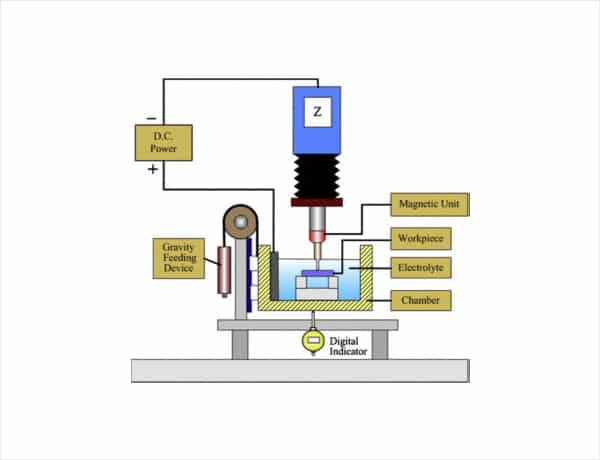
2.Chemical Micro Machining
- Reactive ion etching (RIE): is a kind of plasma process in which species are discharge-excited by radio frequency to etch substrates or films in a low-pressure chamber. It is a cooperative process of chemically active species and high-energy ion bombardment.
- Electrochemical machining (ECM): a method of removing metal by the electrochemical process. It is usually used in large-scale production to machine extremely hard materials or materials that are difficult to process by traditional methods. Its use is limited to conductive materials. ECM can cut small or odd-shaped angles, complex profiles, or cavities in hard and exotic metals.
3.Mechanical Micro Machining
- Diamond turning: a process of turning or mechanical machining of precision elements using lathes or derivative machine tools equipped with natural or synthetic diamond-tipped tool bits.
- Diamond milling: a type of cutting process, can be used to generate aspheric lens arrays by annulus cutting methods with a spherical diamond tool.
- Precision grinding: a type of abrasive machining, allows workpieces to be machined to fine surface finishes and very close tolerances, achieving tolerances of 0.0001″.
- Polishing: a type of abrasive machining, argon ion beam polishing is a fairly stable process that is used for finishing telescope mirrors and correcting residual errors of mechanically polished or diamond-turned optics, and the MRF process is the first deterministic polishing process that has been commercialized and is employed for the production of aspherical lenses, mirrors, etc.
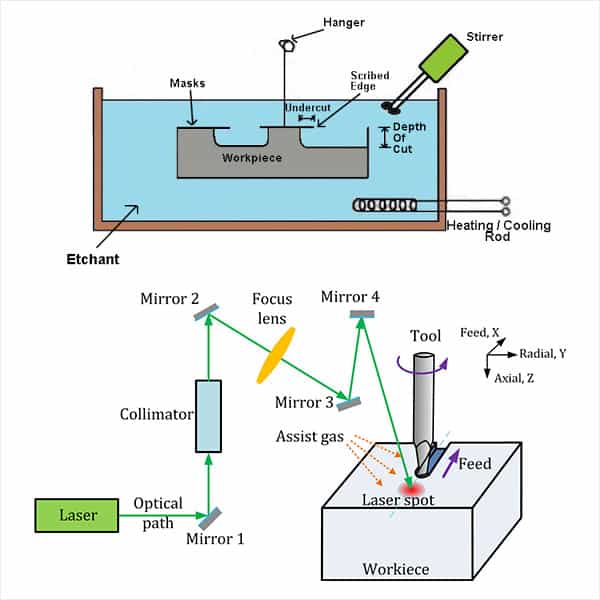
Benefits & Advantages of Micromachining
- – Versatility. Micromachining is applicable for the production of both prototypes and parts with micro features, made from metals and plastics.m
- – Efficiency. Micro parts can be fabricated quickly, it offers a solution of single process machining, which reduces the machines required and shortens the lead time.
- – Repeatability. Micromachining can repeatedly produce small, intricate components with high precision and tight tolerances.
- – Applications. Micromachining allows a greater range of parts to be made, even larger parts with higher accuracy and speed can be machined on the equipment for micromachining.
Applications of Micro Machining
Many industries are following the trend of using micro parts in different applications, including medical parts, electronic components, particle filters and pieces for other fields.
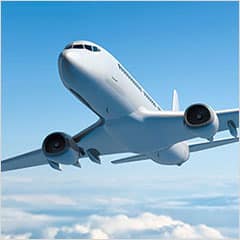
Aircraft and aerospace
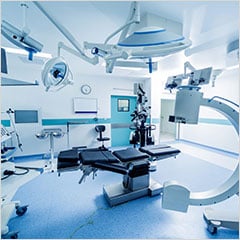
Medical devices
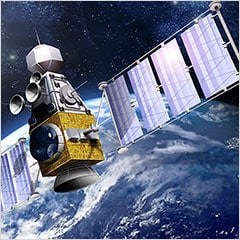
Military satellites
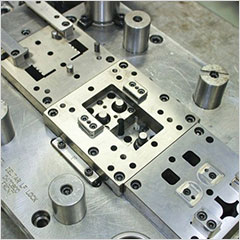
Tools and dies
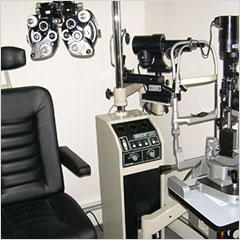
Optical equipment
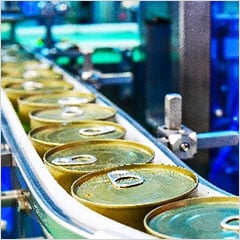
Food manufacturing
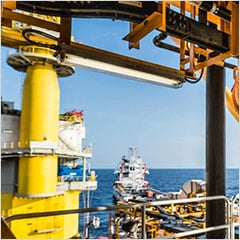
Oil and gas
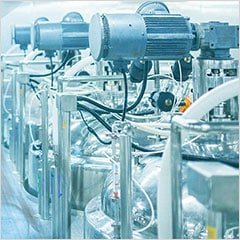
Pharmaceutical
Equipment and Machines Used in Micro Machining
- Sinker EDM center: used to produce small, unusual shapes and micro parts requiring intricate details, available materials including ferrous and non-ferrous metals.
- Wire EDM machines: offers extremely find EDM micro machining, produces the finest plunge patterns using 0.001” diameter cutting wire.
- CNC Swiss lathes: manufactures parts with the tightest tolerances and exact specifications, versatile for a diversity of components to suit the demand of any industry. Typical industries are medical, optical, aerospace, and military.
- 5-axis micro milling/machining center: to achieve the highest precision results, repeatable accuracy of the micro machining parts.