Processes
- Polymer Processing
- Injection Molding Insert Molding Blow Molding Over Molding Metal Injection Molding Thermoforming
- Metal Casting
- Die Casting Castings & Forgings Wax Casting Lost Wax Casting Grey Iron Castings Centrifugal Casting Investment Casting Permanent Mold Sand Casting Shell Mold Casting Aluminum Investment Casting Brass Investment Casting Steel Investment Castings Titanium Investment Casting
- Machining
- Milling Turning EDM machining CNC Engraving Hole-making Tap Size Chart Drill Size Chart 5 axis machining Micro Machining CNC Cutting Metal Processes Ceramic Manufacturing Swiss Precision Machining
Materials
What Is Blow Molding
Blow molding is a rapidly developing plastic processing method. The tubular plastic blank obtained by extrusion or injection molding of thermoplastic resin is placed in the split mold when it is hot (or heated to a softened state). After closing the mold, compressed air is injected into the blank immediately to make the plastic blank inflate and cling to the inner wall of the mold. After cooling and demoulding, various hollow products are obtained.
Blow molding began to be used in the production of LDPE vials during the Second World War. In the late 1950s, with the birth of HDPE and the development of blow molding machine, blow molding technology has been widely used. The volume of the hollow container can reach thousands of liters, and some production has been controlled by computer. Polyethylene, polyvinyl chloride, polypropylene and polyester are suitable for blow molding. The hollow containers are widely used as industrial packaging containers.
According to the parison making method, blow molding can be divided into extrusion blow molding and injection blow molding, and the newly developed ones are multi-layer blow molding and stretch blow molding.
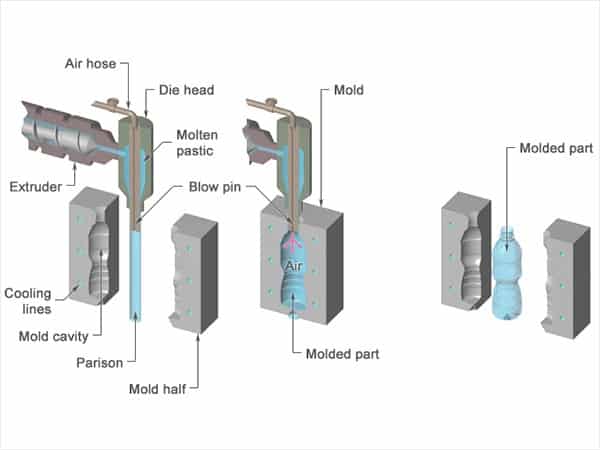
Common Types Of Blow Molding
Extrusion blow mo lding
An extruder forces molten plastic through a die head, which forms the parison around a blow pin, with the help of a rotating screw. The parison is extruded vertically between the two open mold halves, allowing the parison and blow pin to shut between them. To inflate the parison, pressurized air is forced through the blow pin. This is the most prevalent type of blow molding, and it is used to produce vast amounts of very simple parts in big quantities.
Injection blow molding
To make a hollow parison, molten plastic is injection molded around a core inside a parison mold. Both the parison and the core are transferred to the blow mold and securely fastened when the parison mold opens. The core then opens, allowing a stream of compressed air to fill the parison. Because of the reduced production rate, this approach is less widely utilized, but it is capable of creating more sophisticated pieces with greater accuracy. For small, intricate bottles, such as those used in medical purposes, injection blow molding is frequently preferred.
Stretch blow molding
It’s similar to injection blow molding in that the parison is formed in the same way. However, it is heated and stretched downward by the core before being inflated after it is transported to the blow mold. The plastic gains more strength as a result of this stretching. Stretch blow molding is commonly used to manufacture products that must bear internal pressure or be extremely durable, such as soda bottles.
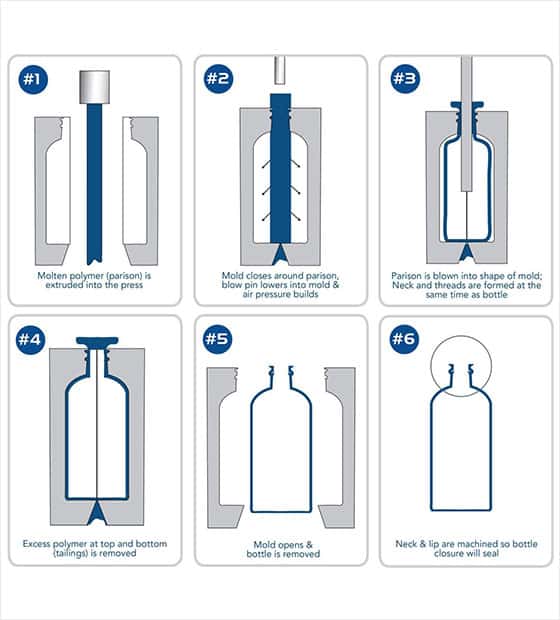
Properties
Shapes: Thin-walled: Cylindrical, Cubic, Complex
Part Size: Envelope: Up to 105 ft³
Materials: Thermoplastics
Surface finish – Ra: 250 – 500 μin
Tolerance: ± 0.04 in.
Max wall thickness: 0.015 – 0.125 in.
Quantity: 100000 – 1000000
Lead time: Days
Advantages & Disadvantages Of Blow Molding
Pros:
- Can form complex shapes with uniform wall thickness
- High production rate
- Low labor cost
- Little scrap generated
Cons:
- Limited to hollow, thin walled parts with low degree of asymmetry
- Poor control of wall thickness
- Poor surface finish
- Few material options
- High tooling and equipment cost
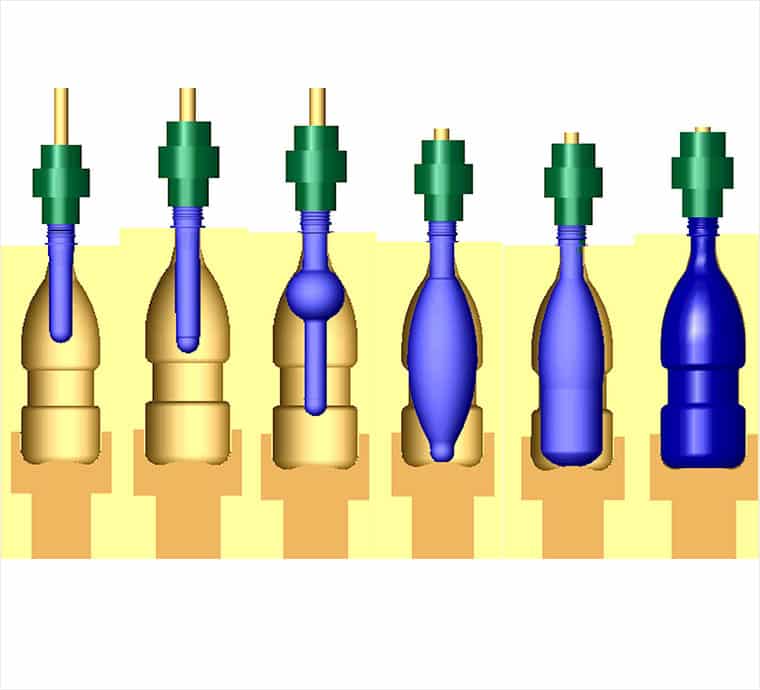
Blow Molding Applications
Commonly, blow molded products are used for people’s daily necessities such as bottles, jars, baby products, containers, ducting, sporting goods, etc.
Blow Molding Capabilities | ||
---|---|---|
Typical | Feasible | |
Shapes: | Thin-walled: Cylindrical Thin-walled: Cubic Thin-walled: Complex |
|
Materials: | Thermoplastics |
|
Surface finish – Ra: | 250 – 500 μin | 250 – 500 μin |
Tolerance: | ± 0.04 in. | ± 0.01 in. |
Max wall thickness: | 0.015 – 0.125 in. | 0.01 – 0.24 in. |
Advantages: | Complex shapes with uniform wall thickness can be formed Low labor cost Productivity is high Little scrap generated |
|
Disadvantages: | It is limited to hollow thin-walled parts with low asymmetry Poor wall thickness control Few material options Tools and equipment cost a lot |
|
Applications: | Bottles, containers, pipes |