Processes
- Polymer Processing
- Injection Molding Insert Molding Blow Molding Over Molding Metal Injection Molding Thermoforming
- Metal Casting
- Die Casting Castings & Forgings Wax Casting Lost Wax Casting Grey Iron Castings Centrifugal Casting Investment Casting Permanent Mold Sand Casting Shell Mold Casting Aluminum Investment Casting Brass Investment Casting Steel Investment Castings Titanium Investment Casting
- Machining
- Milling Turning EDM machining CNC Engraving Hole-making Tap Size Chart Drill Size Chart 5 axis machining Micro Machining CNC Cutting Metal Processes Ceramic Manufacturing Swiss Precision Machining
Materials
As one of the special castings, centrifugal casting has occupied a very important position in the modern foundry industry.
What is Centrifugal Casting?
Centrifugal casting or rotocasting is a casting method in which liquid metal is poured into a rotating mold (usually 250-1500r/min). Under the action of centrifugal force, the mold rotates at a high speed to complete the filling and solidification of the molten metal.
These high rotational forces and the solidification directed from the outside inwards create a particularly dense and pure structure. Impurities and gas inclusions are driven to the surface and can be easily removed in the subsequent processing.
Products manufactured using the centrifugal casting process therefore have excellent technological properties that are far superior to static casting in many areas and are comparable to forging quality.
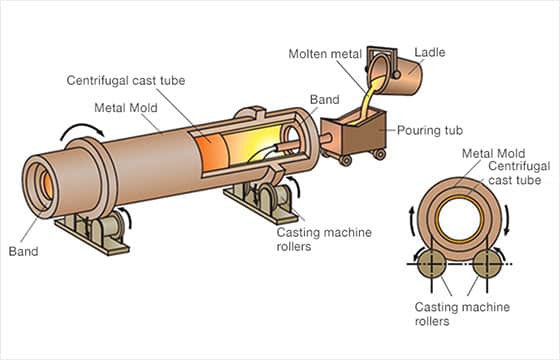
Centrifugal Casting Machines
In order to achieve the above process, a centrifugal casting machine must be used to create conditions for the casting to rotate. According to the different spatial position of the mold rotating shaft, the centrifugal casting machine can be divided into two types: bedroom centrifugal casting machine and vertical centrifugal casting machine.
Vertical Centrifugal Casting Machine
It is mainly used to produce ring castings whose height is less than the diameter, and sometimes this type of centrifugal casting machine can also be used to pour heterogeneous castings.
On a vertical centrifugal casting machine, the mold is rotated around a vertical axis. Due to the centrifugal force and the gravity of the liquid metal, the inner surface of the casting is parabolic, causing the casting to be thinner and thicker. Under other conditions unchanged, the higher the height of the casting, the greater the difference in wall thickness. Therefore, vertical centrifugal casting is mainly used for castings smaller than the diameter of the disc ring, and because the wall thickness is uneven under the gravity of the liquid metal itself, the subsequent cutting process must be increased.
Because it is more convenient to install and stabilize the mold on the vertical casting machine, not only the metal mold can be used, but also the sand mold, the molten mold shell and the non-metallic mold can be used.
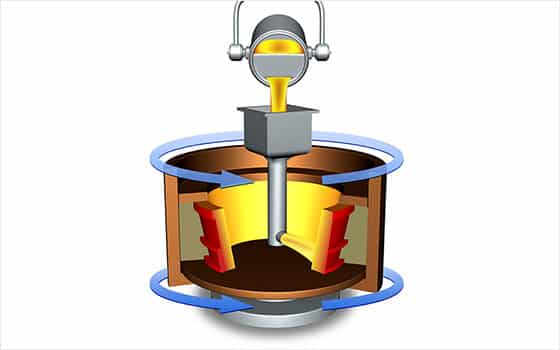
Horizontal Centrifugal Casting Machine
It is mainly used to produce casing and pipe castings larger than the diameter, and the mold is rotated around the horizontal axis.
In the horizontal centrifugal casting machine, the mold is rotated around a horizontal axis. The cooling conditions of each part of the casting are basically the same, so it is possible to cast cylindrical and pipe sleeves with uniform wall thickness.
Centrifugal Casting Process Types in Detail
In the centrifugal casting process, the steel is poured through the centrifugal axis into a mold that rotates. Due to the up to 120 times acceleration due to gravity, the steel solidifies, creating a particularly pure and dense structure. Gas inclusions and impurities are driven to the surface so that they can be removed during the subsequent processing. For this reason, the parts produced have excellent technological properties.
Horizontal Casting For Better Properties
Horizontal casting leads to better properties such as a homogeneous structure with an isotropic behavior, excellent machinability and low internal stress. In this process, the melt is poured into a horizontal mold (often made of steel or cast iron), which is closed at the front and back with lids. The mold is often lined with a protective layer made of ceramic (coating).
In the case of particularly long castings or continuous centrifugal casting, the casting channel can be moved during the casting process with horizontal casting. This enables smooth outer contours, cast-on collars, slightly conical contours or shoulders. Due to the centrifugal force, the inner surface is cylindrically smooth.
The dimensions of the cast parts depend heavily on the material and other technical constraints. With the process, internal diameters from 20 mm, but often only from 40 mm, are economical. The wall thickness should not be greater than the inner diameter. However, that depends on the material.
The outside diameter is almost unlimited, but in practice it is often limited to 1200 mm. The length of the horizontal cast parts depends on the inside diameter and the material and is between 1.5xd and a maximum of six meters.
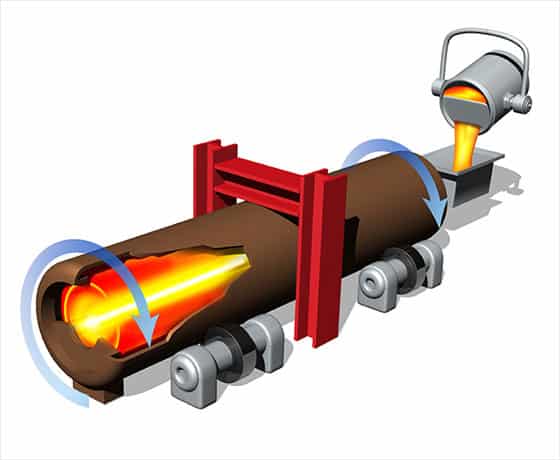
Vertical Casting – Time and Cost saving Option For Model Casting
Vertical casting is mainly used for spherical or conical outer contours. In this process, the melt is poured into a mold, the axis of which rotates vertically. The speed of rotation is significantly slower than with horizontal casting. The combination of gravity and centrifugal force forms a parabola on the inner surface, which can be adjusted via the speed. The inner contour can also be controlled via the casting weight.
Composite Casting – Casting Process With Different Casting Materials
In composite casting, several layers of casting materials are poured on top of one another during the solidification process. Made in horizontal casting, products can be created that combine the properties of different steels. This allows the transition of the materials to take place in fine gradations. The disadvantage is that the inner material is alloyed with the remaining, liquid material of the outer material when it is cast. As a result, the possibility of combining materials is limited. One advantage is the significantly higher productivity and the greater wall thickness of the outer layer.
Centrifugally Cast Pipes for Use at High Temperatures
Special tubes are used in petrochemicals as well as in the heat treatment and steel industries. Compared to forged tubes, they have better properties at higher temperatures.
In the casting process for centrifugally cast pipes, it is possible to introduce a higher carbon content, which results in a coarser grain. This results in higher values for the yield point and strength. For these reasons, centrifugally cast tubes are preferred for use at high temperatures.
Another advantage is that the centrifugal forces cause contamination to be deposited on the inside of the pipe. This creates a homogeneous quality and uniform structure in the pipe wall. If necessary, the centrifugally cast pipes can be drilled in the inner diameter to remove the contamination.
Centrifugal Casting with Stainless Steel
In principle, anything can be made of stainless steel using the centrifugal casting process. The prerequisite is that the part to be produced has a hole in the middle.
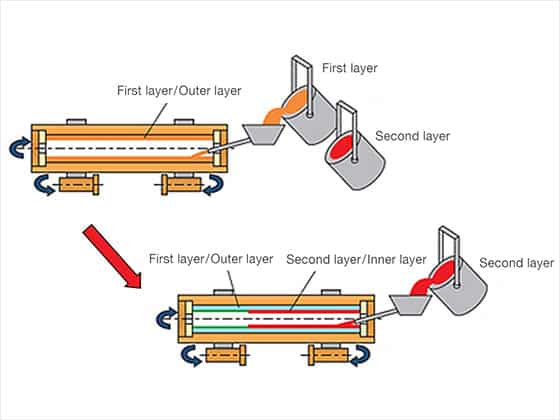
Centrifugal Casting Plastic for Thick-Walled Plastic Figures
Centrifugal casting is also used to make thick-walled plastic figures. These manufacturing processes are also suitable for smaller batch sizes.
Centrifugal Casting Application in Dental Technology for Shape Images
Centrifugal casting has also established itself in dental technology. The process enables casting and shape mapping with smaller amounts of alloy.
Here the process makes use of the centrifugal force created by the mass of the alloy, the radius of the sling arm and the number of revolutions per minute. Normally, the number of revolutions and the radius of the sling arm are often predetermined by the design of the casting equipment, i. H. that the dental technician can only influence the centrifugal force or the shape mapping through the amount of alloy used – a disadvantage of centrifugal casting.
Centrifugal Casting Bronze
Cast parts made of bronze are also possible. The main products here are rings, gears, beeches and reduction gears. They are particularly convincing due to their lower porosity, smaller grain size (-> more uniform ratio between ductility and toughness in the material) and purity.
Features of Centrifugal Casting (Advantages)
Since during centrifugal casting, liquid metal is filled with the mold and solidified while rotating, centrifugal casting has the following characteristics:
- Liquid metal can form a hollow cylindrical free surface in the mold, so that hollow castings can be cast without a core, which can effectively simplify the production process of barrel and tube castings;
- Due to the centrifugal force generated by the liquid metal during rotation, the centrifugal casting process can significantly improve the metal filling capacity, so some alloys with poor fluidity and thin-walled castings can be produced by centrifugal casting;
- Due to the centrifugal force, the feeding conditions are improved, and the gas and non-metallic inclusions are also easy to be discharged from the liquid metal.
The structure of this centrifugal casting is denser, with fewer defects such as shrinkage holes (shrinkage porosity), pores, and inclusions; - Centrifugal casting does not require sprue orifice, and does not require casting riser. When casting hollow castings, the core can be omitted, and the metal utilization rate can reach 80%-90%, which reduces production costs and improves production efficiency.
- It is convenient to cast “bimetal” castings, such as inserting and casting copper lining in the steel sleeve, the bonding surface is firm, wear-resistant, and copper alloy can be saved.
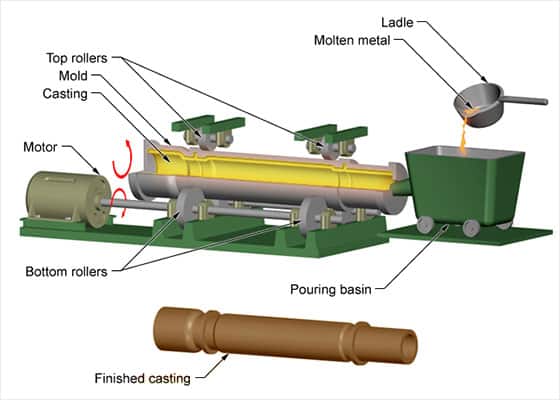
Defects of Centrifugal Casting (Disadvantages)
There are many advantages of centrifugal casting, but when casting some pipe sleeve components made of alloy materials, defects such as incomplete filling, pores on the surface, sand, cracks, slag inclusion, and needle punches on the surface will appear. Introduce its main defects. To
- Crack defects: When casting pipe castings, sometimes horizontal and vertical cracks appear. Among them, transverse cracks are the majority. Longitudinal cracks mainly occur when the metal mold is rotated at a high speed by the centrifuge. The mold itself will produce a certain vibration, which will cause the metal to crack when it is cooled and crystallized, because the temperature of the casting is relatively high. High, low strength, but in the actual production process, the most horizontal cracks appear. These cracks often appear at the end of the pipe. The pipe castings are easy to crack when they are out of the mold, and they may even break along the center position. The speed of the mold must be controlled well in the middle. To
- The filling is incomplete. There are usually two cases of incomplete filling in centrifugal cast steel pipes: the first is that the filled metal liquid is not enough, which causes the size of the pipe sleeve components to become smaller; the second is the uneven wall thickness of the pipe, which is such a defect It is especially obvious when casting pipe sleeve castings with a wall thickness of 7 to 8 mm, so special attention should be paid to the value of the length to diameter ratio of the pipe sleeve (L/D>15). To
- Stomatal defects. Such defects mainly exist on the inner surface of the pipe sleeve type components, and the diameter is small, generally 0.25mm ~ 3mm, the depth is 0.4mm ~ 2.5mm, and the density is relatively high. It often appears as a flaky area. To
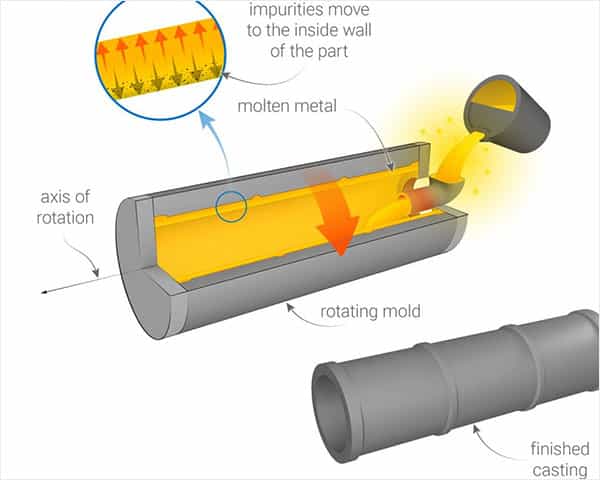
- Sand inclusions on the surface of the steel pipe. A rough pitted surface and a slight bulge appear locally on the surface of the steel pipe, and the rough pitted surface has a clear peripheral contour. In severe cases, it becomes a ring-shaped belt-like sand inclusion. When the rough steel surface layer is removed, a thin coating layer, that is, sand inclusions, can be seen. Sand inclusions can be removed after 1mm~2mm processing. But it seriously affects the quality of the cast skin. If the steel pipe is not processed, it is likely to be scrapped. This defect mostly occurs in steel pipes with paint. To
- Needle punching on the end face of the casting. When casting pipe castings, when thicker coatings are applied, needle-like burrs will appear on the end surface of the casting, with a diameter of 0.5 mm to 1 mm, a height of 2 mm, and a higher density. , If there are 3, 4, 5, etc. defects, the machining allowance should be increased.
Application of the Centrifugal Casting
Parts that are created using this casting process are used for many applications:
- As a decanter in the pharmaceutical, biotechnical and food industry, for sewage sludge and paint sludge treatment, plastic recycling and cooling emulsion processing (possible components: end walls, seal carriers, conical and cylindrical drum shells, screw bodies, pipes, sealing covers, screw body parts)
- As valve seat rings in the inlet and outlet area for large diesel engines for ships and stationary power generators (possible components: inlet valve and outlet valve seat rings)
- In continuous casting systems for bloom, slab, billet and beam blank systems (possible components: strand guide rollers for all segments of the continuous casting systems)
- For the production of concrete sewer pipes